Workers Comp Insurance California For Industrial Buildings
Index
Understanding Workers' Comp Insurance
California's Workers' Comp Insurance Laws
How to Obtain Workers' Comp Insurance in California
Costs Associated with Workers' Comp Insurance
Filing a Workers' Comp Insurance Claim in California
Contact Us
Phone
886-226-4436
Location
9340 Bolsa Ave, Westminster, CA 92683
Workers Comp By City
Industrial Buildings: The Foundation of Modern Industry
Industrial buildings are essential to the growth and success of various industries, providing the necessary infrastructure to facilitate production, storage, and distribution. These structures house manufacturing plants, warehouses, and research facilities, playing a crucial role in industrial operations. With advancements in construction materials, automation, and energy efficiency, industrial buildings continue to evolve, ensuring better functionality, sustainability, and economic viability.
Why Industrial Buildings Are Essential
Industrial buildings serve as the backbone of many industries. Here’s why they remain indispensable:
Efficiency and Functionality
- Designed to optimize workflow and minimize production downtime.
- Large open spaces accommodate machinery, conveyor systems, and storage areas.
- Strategic layouts improve accessibility and logistical efficiency.
Structural Durability and Safety
- Built with high-strength materials like steel, reinforced concrete, and advanced composites.
- Equipped with fire suppression systems, ventilation, and safety exits.
- Seismic-resistant designs ensure longevity and protection against natural disasters.
Sustainability and Green Initiatives
- Many industrial buildings integrate solar panels and energy-efficient lighting.
- Use of recyclable materials reduces environmental impact.
- Implementation of rainwater harvesting and waste management systems.
Scalability and Adaptability
- Modular designs allow for future expansion and repurposing.
- Can be customized to accommodate new technologies and production needs.
- Adaptable layouts cater to evolving industry requirements.
Key Features of a Successful Industrial Building
A well-designed industrial building possesses distinct characteristics that ensure efficiency, functionality, and sustainability.
Advanced Construction Materials and Techniques
- Use of prefabricated steel structures for quick assembly.
- High-performance insulation materials enhance energy efficiency.
- Corrosion-resistant coatings increase the lifespan of metal structures.
Strategic Location and Accessibility
- Proximity to highways, ports, and railway networks facilitates transportation.
- Adequate parking space and docking stations for freight handling.
- Compliance with zoning regulations and environmental standards.
Smart Technology Integration
- IoT-enabled monitoring for real-time energy consumption tracking.
- Automated climate control and air purification systems.
- AI-driven security surveillance for enhanced protection.
Sustainability and Energy Efficiency
- LEED-certified buildings promote eco-friendly construction practices.
- Solar panels, LED lighting, and geothermal heating reduce carbon footprint.
- Rainwater harvesting and greywater recycling systems for sustainable water management.
Types of Industrial Buildings
Industrial buildings come in various forms, each serving specific functions. Here are the most common types:
Manufacturing Plants
- Facilities designed for mass production and assembly of goods.
- Equipped with conveyor belts, robotic arms, and heavy-duty machinery.
- Used in industries like automotive, electronics, and pharmaceuticals.
Warehouses and Distribution Centers
- Large storage spaces for inventory management and logistics.
- Advanced racking systems optimize space utilization.
- Cold storage warehouses cater to perishable goods.
Research and Development (R&D) Facilities
- Dedicated spaces for innovation, prototyping, and product testing.
- Equipped with laboratories, clean rooms, and specialized testing equipment.
- Used by pharmaceutical, aerospace, and tech industries.
Data Centers
- Buildings that house servers, cloud storage, and IT infrastructure.
- Require advanced cooling systems and uninterrupted power supply.
- Essential for digital businesses, banking, and telecommunications.
Processing Plants
- Facilities designed for refining raw materials into usable products.
- Common in food processing, chemical production, and metallurgy.
- Require specialized ventilation, waste disposal, and safety measures.
Common Applications of Industrial Buildings
Industrial buildings are utilized in a variety of sectors, supporting production, logistics, and technological advancements.
Manufacturing Industry
- Houses assembly lines for automotive, aerospace, and electronics industries.
- Enables large-scale production and quality control measures.
- Incorporates automated processes for efficiency.
Logistics and Supply Chain Management
- Warehouses store and distribute goods efficiently.
- Distribution centers streamline e-commerce and retail fulfillment.
- Strategic locations ensure fast delivery and inventory management.
Food Processing and Storage
- Cold storage facilities preserve perishable goods.
- Hygienic processing plants maintain food safety standards.
- Automated packaging and labeling systems enhance efficiency.
Pharmaceutical and Healthcare
- Specialized facilities for drug manufacturing and research.
- Clean rooms ensure controlled environments for sensitive production.
- Compliance with strict health regulations and safety standards.
Technology and Data Management
- Data centers support cloud computing and IT infrastructure.
- Secure storage of digital information and backup systems.
- High-tech facilities with precision climate control.
Future Trends in Industrial Buildings
Industrial buildings are continuously evolving with technological advancements and sustainability initiatives. Here are key trends shaping the future:
Smart and Automated Industrial Spaces
- Integration of AI-driven robotics for automated production.
- Smart sensors for predictive maintenance and real-time monitoring.
- Automated climate control for energy-efficient operation.
Sustainable Construction Practices
- Use of carbon-neutral materials in building design.
- Implementation of energy-efficient windows and roofing systems.
- Eco-friendly insulation materials to reduce heating and cooling costs.
Hybrid Industrial Complexes
- Multi-functional buildings combining manufacturing, office spaces, and R&D.
- Flexible spaces for companies requiring diverse operations under one roof.
- Encourages innovation and collaboration across industries.
3D Printing in Construction
- Additive manufacturing techniques used for rapid industrial building construction.
- Reduces construction waste and labor costs.
- Allows for more innovative and cost-effective building designs.
Resilient and Disaster-Proof Structures
- Advanced materials designed to withstand extreme weather conditions.
- Seismic-resistant frameworks to protect against earthquakes.
- Floodproofing and fireproofing measures for added safety.
Industrial Buildings: Key Aspects of Construction and Design
Industrial buildings play a crucial role in economic growth and development. These structures house manufacturing plants, warehouses, distribution centers, and processing facilities. Designed to optimize productivity, safety, and efficiency, industrial buildings cater to a variety of industries such as automotive, aerospace, logistics, and consumer goods. Below are the key aspects that define successful industrial buildings.
1. Types of Industrial Buildings
Warehouses
Warehouses are storage facilities designed for inventory management, logistics, and distribution. They feature high ceilings, large open spaces, and loading docks to facilitate efficient storage and movement of goods.
Manufacturing Plants
Manufacturing plants are specialized facilities equipped with production lines, assembly units, and heavy machinery. They vary in design based on the industry they serve, such as automotive, electronics, or pharmaceuticals.
Cold Storage Facilities
Cold storage buildings are temperature-controlled structures used for storing perishable goods like food, pharmaceuticals, and chemicals. These buildings require insulated walls, refrigeration systems, and humidity control mechanisms.
Data Centers
With the rise of digital infrastructure, data centers have become a key component of industrial real estate. These facilities house servers, networking equipment, and power backup systems, ensuring uninterrupted data processing and
storage.
R&D Facilities
Research and development (R&D) buildings are designed for innovation and testing. Industries like biotechnology, aerospace, and automotive require specialized labs, clean rooms, and advanced machinery to conduct experiments and develop new technologies.
2. Material Selection in Industrial Buildings
Selecting the right materials is critical for the durability, efficiency, and sustainability of industrial buildings. Common materials include:
Steel
- High strength and durability
- Ideal for large-span structures
- Fire and corrosion-resistant
Concrete
- Provides structural stability
- Excellent thermal mass for temperature control
- Used in flooring, foundations, and walls
Insulated Panels
- Commonly used in cold storage and clean rooms
- Improves energy efficiency
- Reduces noise levels
Glass and Aluminum
- Used for office spaces within industrial buildings
- Enhances natural lighting
- Reduces energy consumption through efficient insulation
3. Design Considerations for Industrial Buildings
Efficient industrial buildings incorporate several key design elements:
Space Utilization
- Optimized layout to improve workflow and material handling
- Adequate space for storage, production, and employee movement
Structural Integrity
- Buildings must withstand heavy loads, vibrations, and environmental factors
- Reinforced foundations to support heavy machinery
Ventilation and HVAC Systems
- Essential for air quality and temperature control
- Critical for facilities handling chemicals, fumes, or extreme temperatures
Safety Features
- Fire-resistant materials and sprinkler systems
- Emergency exits and clear signage
- Proper lighting and anti-slip flooring
4. Importance of Industrial Buildings in Economic Growth
Industrial buildings contribute significantly to local and global economies:
Job Creation
- Employing workers in manufacturing, logistics, and facility management
Boosting Trade
- Warehouses and distribution centers facilitate the movement of goods across borders
Technological Advancements
- Providing spaces for innovation in automation, AI, and robotics
5. Key Features of an Efficient Industrial Facility
A well-optimized industrial facility enhances productivity while reducing costs. Essential features include:
Automation and Smart Technologies
- Integration of Industry 4.0 principles
- IoT-enabled systems for monitoring equipment and inventory
Modular Design
- Allowing for future expansion and adaptability
- Quick installation and relocation of machinery
Energy Efficiency
- Solar panels and LED lighting to reduce energy consumption
- Smart HVAC systems for optimized temperature control
6. Sustainability in Industrial Buildings
Modern industrial facilities prioritize eco-friendly practices to reduce their environmental footprint:
Green Building Certifications
- LEED (Leadership in Energy and Environmental Design) certification for sustainable construction
- Use of recyclable and low-impact materials
Waste Management
- Implementation of recycling programs for metal, plastic, and industrial by-products
- Proper disposal of hazardous materials
Water Conservation
- Rainwater harvesting and water-efficient plumbing fixtures
7. Challenges in Industrial Construction
Despite their benefits, industrial buildings face several challenges:
High Initial Costs
- Advanced machinery and high-quality materials require substantial investment
Regulatory Compliance
- Adhering to local zoning laws, fire safety regulations, and environmental guidelines
Infrastructure Limitations
- Industrial zones require proper road networks, power supply, and water access
8. Strategies for Optimizing Industrial Building Performance
To maximize efficiency and longevity, industrial buildings incorporate the following strategies:
Preventive Maintenance
- Regular inspections and servicing of machinery and structural components
Digital Twin Technology
- Creating virtual simulations to predict performance and maintenance needs
Employee Training
- Ensuring workers are equipped with the necessary skills to operate advanced machinery
9. Investment Opportunities in Industrial Real Estate
With the growing demand for logistics and manufacturing spaces, industrial real estate offers lucrative investment
opportunities:
E-commerce Warehousing
- Rising online shopping trends fuel demand for large storage facilities
Smart Factories
- Investment in automated and AI-driven industrial spaces
Renewable Energy Facilities
- Industrial buildings designed for solar and wind energy production
10. Future Trends in Industrial Building Design
The industrial sector is evolving, with new trends shaping the future of industrial buildings:
Robotics and AI Integration
- Automation reducing reliance on human labor
- AI-driven predictive maintenance for equipment longevity
Sustainable and Net-Zero Buildings
- Industrial buildings focusing on carbon-neutral operations
- Advanced insulation and energy-efficient materials
Multi-Purpose Industrial Spaces
- Flexible spaces accommodating different functions (e.g., manufacturing + warehousing)
Smart Logistics and Supply Chain Integration
- AI-based demand forecasting and real-time tracking of goods
Understanding Industrial Buildings
Industrial buildings are specialized structures designed to support the wide array of activities involved in manufacturing, processing, storage, and distribution. They often feature expansive floor areas, high ceilings, robust construction materials, and flexible interior layouts to accommodate heavy machinery, large inventories, and complex workflows. These buildings serve as the backbone of modern industry—enabling manufacturers, logistics companies, and various other businesses to efficiently operate on both a local and global scale.
The primary goals of industrial buildings typically include:
- Functionality: Ensuring that the layout and design support the intended use—whether it’s heavy manufacturing, light assembly, or warehousing.
- Durability: Utilizing materials and construction techniques that can withstand constant use, vibrations from machinery, and extreme weather conditions.
- Scalability: Offering room for expansion or easy reconfiguration as operations grow or change.
- Energy Efficiency: Minimizing operational costs by incorporating energy-saving systems and sustainable design principles.
- Safety and Compliance: Meeting strict building codes and regulations to protect workers, products, and the environment.
As industries evolve to incorporate new technologies like automation and advanced robotics, industrial buildings are also adapting through modern design solutions, smart building systems, and improved sustainability features.
Key Aspects of Industrial Buildings
Just like in manufacturing, where success depends on machinery, materials, workforce, and precision, the effectiveness of an industrial building depends on similar foundational aspects.
Structural Design and Materials
- Steel Framework: Commonly used for its strength, versatility, and relatively quick construction times.
- Concrete Elements: Floors and walls need to endure heavy loads, chemical spills, or temperature fluctuations.
- Roofing Systems: High-grade materials that can handle loading from ventilation units, solar panels, or weather extremes.
Space Planning and Layout
- Open Floor Plans: Large, uninterrupted spaces accommodate assembly lines, product storage, or conveyor systems.
- Zoning: Separates hazardous processes (e.g., chemical handling) from safer areas like offices or employee break rooms.
- Vertical Space Utilization: Incorporating mezzanines, elevated storage racks, or multi-level conveyors to make the most of available room.
Infrastructure and Utilities
- Electrical Systems: Must handle the voltage demands of heavy machinery or high-tech equipment.
- HVAC and Ventilation: Essential for maintaining air quality, especially where dust, fumes, or extreme temperatures are concerns.
- Plumbing and Water Management: Includes drainage systems that can handle industrial-scale water usage and waste.
- Fire Safety Systems: Sprinklers, fire walls, and detection systems to meet safety codes and insurance requirements.
Workforce Requirements
- Employee Facilities: Offices, locker rooms, rest areas, and adequate restroom facilities.
- Accessibility: Compliance with local regulations for disabled access.
- Safety Measures: Clearly marked walkways, emergency exits, and signage reduce the risk of accidents.
Technology Integration
- Automation and Robotics: Industrial buildings increasingly feature robotic arms, automated guided vehicles (AGVs), and sensor-based systems for productivity.
- IoT and Data Management: Sensors and software monitor building performance—tracking energy consumption, equipment status, and environmental conditions in real time.
- Security Systems: Access control, CCTV cameras, and intrusion detection help protect valuable assets.
Importance of Industrial Buildings in Society
Industrial buildings serve as more than just physical structures; they catalyze progress in multiple areas of human life and economic development.
- Economic Growth
- Job Creation: Construction, maintenance, and day-to-day operations offer employment opportunities.
- Local and Global Supply Chains: Industrial buildings house the activities that keep goods moving—from raw materials to finished products.
- Technological Innovation
- Research and Development: Specialized labs within industrial complexes are crucial for prototyping new technologies.
- Automation Hubs: Factories with cutting-edge robotics often drive advancements in engineering and software.
- Infrastructure Development
- Supporting Public Works: Many industrial buildings produce materials (like steel beams, cement, or construction components) essential for infrastructure projects.
- Distribution Network: Warehouses and logistics centers ensure the timely delivery of products worldwide.
- Community and Social Impact
- Education and Training: Industrial facilities often partner with local institutions to provide vocational programs, apprenticeships, and skill-based training.
- Resource Availability: Manufacturing plants for food, textiles, or medical supplies play a direct role in community well-being.
Types of Industrial Buildings
Industrial buildings can be broadly categorized based on their core function, scale, and the industry they serve:
- Manufacturing Plants
- Heavy Industrial: Foundries, steel mills, and automotive assembly lines that require robust structural support.
- Light Industrial: Electronics assembly or precision part machining, which demand cleaner, more controlled environments.
- Warehouses and Distribution Centers
- Storage Warehouses: Focus on racking systems, inventory management, and easy loading/unloading.
- Fulfillment Centers: Large-scale operations that utilize automation to process online orders swiftly.
- Data Centers
- Mission-Critical Facilities: Require advanced cooling, power redundancy, and security to house servers and computing hardware.
- Research and Development (R&D) Facilities
- Labs and Testing Areas: Designed for innovation in pharmaceuticals, aerospace, electronics, and more.
- Pilot Plants: Smaller-scale industrial setups to test new manufacturing processes before full-scale production.
- Specialized Industrial Structures
- Food Processing Plants: Maintain strict hygiene and climate control standards.
- Cold Storage Facilities: Depend on heavy insulation and advanced refrigeration systems.
Key Design and Construction Processes
Constructing an industrial building involves multiple steps, each critical to ensuring that the final structure meets operational, regulatory, and sustainability targets.
- Site Selection and Feasibility Studies
- Zoning Regulations: Verify that local laws permit industrial use.
- Environmental Assessments: Check for soil stability, flood risks, and wildlife considerations.
- Logistical Considerations: Proximity to transportation (highways, rail lines, ports) for easy material flow.
- Architectural and Engineering Design
- Load Calculations: Structural engineers determine load-bearing requirements for machinery and storage.
- Utility Planning: Designing electrical, water, and ventilation systems to handle industrial-scale demands.
- Sustainable Strategies: Incorporating daylighting, green roofs, or solar panels for energy efficiency.
- Construction and Project Management
- Permits and Approvals: Coordinating with local authorities for building permits, environmental clearances, and inspections.
- Procurement and Scheduling: Ensuring materials arrive on time and that construction stages follow a logical sequence.
- Safety Protocols: On-site measures like harnesses, scaffolding, and hazard training reduce accidents.
- Final Testing and Commissioning
- Systems Integration: Verifying that HVAC, electrical, fire safety, and automation systems work cohesively.
- Occupancy Permits: Formal approval confirming the building meets all code requirements.
- Operational Training: Orienting staff and management on equipment use, emergency procedures, and maintenance routines.
Industry Regulations and Compliance
Regulations ensure industrial buildings maintain standards for safety, quality, and environmental stewardship.
- Building Codes
- Local and National Standards: Regulations like the International Building Code (IBC) guide structural integrity and occupancy limits.
- Fire and Life Safety Codes: Requirements for sprinkler systems, fire alarms, and escape routes.
- Workplace Safety
- OSHA Compliance: Mandates safe working conditions, from machine guardrails to signage for hazardous materials.
- Personal Protective Equipment (PPE): Helmets, safety glasses, or earplugs can be legally required for certain operations.
- Environmental Regulations
- Emissions Control: Factories must adhere to regulations on air pollutants and greenhouse gases.
- Waste Management: Proper disposal or treatment of industrial by-products to reduce environmental impact.
- Sustainability Requirements: Certifications like LEED (Leadership in Energy and Environmental Design) can guide eco-friendly construction.
- Specialized Industry Standards
- Food and Pharma: GMP (Good Manufacturing Practices) for cleanliness and contamination control.
- High-Tech Manufacturing: ISO standards to maintain product quality and consistency.
Challenges in Industrial Buildings
Despite their importance, industrial buildings face several hurdles:
- Rising Construction Costs
- Fluctuating prices for steel, concrete, and other raw materials impact overall budgets.
- Skilled labor shortages can delay projects and increase wages.
- Technological Upgrades
- Integrating advanced automation systems or IoT solutions requires specialized infrastructure, boosting upfront costs.
- Retrofitting older buildings to meet modern standards can be expensive and time-consuming.
- Environmental Pressures
- Balancing industrial-scale energy demands with sustainability goals can be complex.
- Neighbors and local communities may raise concerns about noise, emissions, or increased traffic.
- Regulatory Complexity
- Navigating multiple layers of local, national, and international regulations can slow down construction and operations.
- Companies must stay current with evolving codes and environmental guidelines.
- Location Constraints
- Finding available land near transport hubs while meeting zoning requirements can be challenging.
- Urban sprawl and land-use policies might limit suitable locations for large footprints.
Investment Opportunities in Industrial Buildings
For investors and businesses alike, industrial real estate can be highly attractive:
- Long-Term Leases
- Industrial tenants often sign multi-year agreements, providing stability and predictable returns.
- Diverse Tenant Pool
- Industries ranging from e-commerce and logistics to manufacturing and tech R&D seek industrial space.
- A diversified tenant base can mitigate the risk of vacancy.
- Value-Add Potential
- Upgrading or retrofitting older buildings with modern tech, better insulation, or sustainable features can increase property value and rental rates.
- Strategic Location Advantages
- Proximity to major highways, ports, or urban centers can command higher lease rates and lower turnover.
- Sale-Leaseback Arrangements
- Companies that own their industrial buildings may sell the property to investors and lease it back, freeing up capital for other business needs.
Future Trends in Industrial Buildings
The industrial sector continues to innovate in response to shifting market demands, technological advances, and sustainability objectives:
- Smart Buildings and Automation
- IoT sensors and AI-driven systems allow real-time monitoring of energy use, security, and equipment performance.
- Automated handling systems and robotics streamline processes, from shipping to assembly lines.
- Vertical and Multi-Level Facilities
- As land in urban areas becomes scarcer and more expensive, industrial buildings may expand upward, incorporating multiple floors for manufacturing or storage.
- Sustainable and Green Construction
- Net-zero energy buildings leverage solar panels, energy-efficient HVAC, and other eco-friendly techniques to reduce carbon footprints.
- Innovative materials like cross-laminated timber (CLT) or high-performance concrete lower environmental impact.
- Adaptive Reuse
- Converting older industrial spaces into modern facilities can preserve a site’s historical significance while meeting current building requirements.
- Localized Manufacturing and Distribution
- The rise of on-demand production and rapid fulfillment models drives the need for smaller, tech-forward facilities closer to end consumers.
What Are Industrial Buildings?
Industrial buildings are specialized facilities designed to support large-scale operations, typically involving manufacturing, processing, storage, or distribution of goods. Unlike residential or commercial properties, industrial buildings focus on accommodating heavy machinery, large inventories, and sophisticated logistical systems. Common examples include:
- Factories and Manufacturing Plants
Where raw materials are transformed into finished products. - Warehouses and Distribution Centers
Spaces designed for storing and distributing goods, often featuring extensive shelving systems and docking areas for trucks. - Research and Development (R&D) Facilities
Specialized buildings equipped with labs and testing areas to innovate and improve products or processes. - Data Centers
Facilities housing servers and networking equipment, requiring robust cooling and power systems.
Regardless of their specific use, industrial buildings must meet stringent requirements for structural integrity, safety,
energy efficiency, and environmental impact.
Why Industrial Buildings Are Essential
1. Economic Drivers
Industrial buildings play a vital role in local, regional, and national economies. By providing spaces for manufacturing, logistics, and R&D, these facilities create employment opportunities for skilled and unskilled labor alike. This in turn boosts consumer spending, stimulates growth in surrounding businesses, and attracts further investment.
2. Global Trade and Supply Chain Support
In an increasingly globalized world, efficient supply chains are crucial. Industrial buildings like distribution centers and warehouses form the nodes of these supply chains, ensuring products move smoothly from manufacturers to end consumers. They also facilitate global trade by offering secure and efficient storage and handling processes.
3. Innovation and Technological Advancement
Many industrial buildings house cutting-edge technology, such as robotics, automated storage, and advanced manufacturing equipment. By supporting R&D and high-tech production lines, these facilities drive innovation across industries, helping companies stay competitive.
4. Infrastructure Development
Industrial zones often lead to improved local infrastructure, such as roads, utilities, and telecommunications. As companies expand their operations, they demand better transportation networks and energy systems—benefits that extend to nearby communities.
Key Components of a Successful Industrial Building
Building a successful industrial facility goes beyond erecting four walls and a roof. Key components include:
1. Strategic Site Selection
- Location and Accessibility: Proximity to major highways, ports, or railroads can drastically reduce transportation costs.
- Zoning and Regulations: Compliance with local zoning laws and environmental regulations is crucial to avoid delays or fines.
2. Robust Structural Design
- Foundation and Framing: Industrial buildings must support heavy machinery and large storage racks. Reinforced concrete foundations and high-grade steel framing are common.
- Load-Bearing Capacity: Floors are often designed to handle specific load requirements, especially in manufacturing or warehousing settings.
3. Efficient Layout and Workflow
- Open Floor Plans: Minimizing interior columns and partitions allows flexibility in layout, making it easier to install machinery or reconfigure storage.
- Workflow Optimization: Facilities should be planned to accommodate streamlined processes—placing raw materials, production lines, and finished goods areas in logical sequence.
4. Advanced Building Systems
- HVAC and Ventilation: Maintaining a controlled environment is vital for both product quality (in cases of sensitive materials) and worker safety.
- Power Supply and Backup: Industrial processes often require significant electricity. Backup generators and uninterrupted power supply (UPS) systems are essential for critical operations.
- Fire Safety Systems: Sprinklers, fire alarms, and smoke control systems must be designed to meet or exceed local safety codes.
5. Technology Integration
- Automation and Robotics: Many modern industrial facilities utilize conveyor belts, robotic arms, and autonomous vehicles for material handling and assembly.
- Internet of Things (IoT): Sensors and connected devices provide real-time data on machine performance, inventory levels, and environmental conditions.
- Data Analytics: Gathering and analyzing data can improve productivity, reduce downtime, and enhance supply chain visibility.
6. Sustainability Measures
- Green Building Materials: Using recycled steel or low-carbon concrete reduces environmental impact.
- Energy Efficiency: Solar panels, LED lighting, and energy-efficient HVAC systems help minimize operational costs and carbon footprints.
- Waste Management: Implementing recycling and waste reduction programs can align industrial operations with environmental standards and consumer expectations.
Challenges Faced by the Industrial Building Sector
1. Regulatory and Compliance Hurdles
Industrial buildings must meet stringent health, safety, and environmental regulations. This can involve navigating complex permitting processes and passing regular inspections, which can delay project timelines and add costs.
2. Rising Construction Costs
From raw materials like steel and concrete to skilled labor, the cost of building an industrial facility can be high. Fluctuations in the prices of construction materials can also impact project budgets.
3. Environmental Impact and Sustainability
Industrial operations often result in greenhouse gas emissions and other pollutants. Balancing economic growth with environmental stewardship is a pressing concern for companies, prompting the need for cleaner technologies and sustainable design.
4. Technological Integration and Upgrades
Rapid technological advances mean that industrial buildings must be designed for scalability and flexibility. Retrofitting older facilities with modern systems (like IoT and robotics) can be expensive and disruptive to ongoing operations.
5. Labor Shortages and Skills Gaps
As industrial processes become more automated and digitized, the demand for skilled workers with technical backgrounds rises. Many regions face challenges in finding qualified personnel, impacting productivity and growth.
The Role of Private and Public Entities in Industrial Building
Development
1. Public-Private Partnerships (PPPs)
Governments often collaborate with private developers to facilitate industrial development. Through land grants, tax incentives, or infrastructure improvements, public bodies can attract investment in industrial facilities. In return, companies create jobs and spur economic growth.
2. Regulatory Support and Urban Planning
Local governments shape industrial zones through zoning laws and strategic urban planning. By designating specific areas for industrial use, policymakers help minimize conflicts with residential neighborhoods and streamline the approval process for potential investors.
3. Corporate Social Responsibility (CSR)
Private companies investing in industrial buildings are increasingly mindful of their societal and environmental impact. CSR initiatives might include green building certifications (e.g., LEED), community outreach programs, or partnerships with local educational institutions to train future workforces.
4. Research and Development Funding
Both public agencies and private companies may invest in R&D to develop advanced construction materials, eco-friendly technologies, and improved industrial processes. Grants or venture capital can accelerate the commercialization of cutting-edge solutions, benefiting the entire industrial sector.
Benefits of Well-Managed Industrial Buildings
1. Economic Growth and Job Creation
Efficient industrial buildings can house businesses that offer stable employment, fostering local economies. These facilities can catalyze development in adjacent sectors, like transportation and retail.
2. Improved Operational Efficiency
Modern industrial buildings, optimized for workflow and equipped with advanced technologies, enable faster production cycles, minimized downtime, and reduced operational costs. Automation and data-driven management can further increase productivity.
3. Environmental Sustainability
By implementing energy-saving systems and eco-friendly materials, well-managed industrial buildings reduce their carbon footprint. Some facilities even adopt closed-loop systems, reusing water or byproducts to cut waste and promote a circular economy.
4. Enhanced Community Relations
When industrial developers engage responsibly with communities—addressing concerns like noise, traffic, and pollution—they can foster positive relations and shared benefits. This creates a better operating environment and can attract further investment to the area.
5. Future-Proofing
A well-planned industrial building can adapt to changing technologies or market demands. Flexible floor layouts, modular construction, and scalable utility systems ensure that facilities remain viable for decades.
Future Trends in Industrial Buildings
1. Smart Factories and Digital Transformation
The rise of Industry 4.0 is making industrial buildings more interconnected than ever. Real-time monitoring, predictive maintenance powered by AI, and digital twins are reshaping how facilities are operated and maintained.
2. Modular and Prefabricated Construction
Prefabrication techniques speed up construction and minimize on-site labor. This approach also improves quality control, as building components are produced in controlled factory settings before assembly.
3. Sustainable Innovations
Eco-friendly materials, renewable energy sources, and water-saving systems will become increasingly prominent. With stricter regulations and growing consumer awareness, industrial players are focusing on reducing their environmental impact.
4. Urban Integration
As cities expand and land becomes scarce, industrial zones might need to co-exist more harmoniously with residential areas. Mixed-use developments featuring light industrial, commercial, and recreational spaces can promote balanced urban growth.
5. Flexible and Adaptive Spaces
The future of industrial buildings lies in adaptability. Facilities that can be reconfigured for multiple uses—whether it’s manufacturing, storage, or testing—will be better positioned to meet evolving economic demands and technological changes.
How much does industrial insurance cost?
- Business size: The larger the business or the more employees it has, the higher the premiums could be. Larger operations often have more assets and higher potential liabilities.
- Type of industry: Different industries carry different levels of risk. For instance, manufacturing businesses might pay more than a service-based industry due to the higher likelihood of accidents, equipment damage, or product liability issues.
- Coverage needs: The amount and type of coverage you select—such as general liability, property insurance, workers' compensation, or business interruption insurance—will influence the cost. Comprehensive coverage will naturally cost more than basic policies.
- Location: The geographic location of your business can also impact insurance costs. For example, businesses in regions prone to natural disasters like floods, earthquakes, or hurricanes may face higher premiums.
- Claims history: If the business has a history of frequent claims, it may result in higher premiums, while a clean claims history might help reduce costs.
What type of insurance covers buildings?
The type of insurance that covers buildings is Property Insurance, specifically Commercial Property Insurance for businesses or Homeowners Insurance for residential properties.
For businesses, Commercial Property Insurance covers physical damage or loss to buildings, equipment, inventory, and other property due to events like fire, theft, vandalism, or natural disasters (depending on the policy).
For residential properties, Homeowners Insurance typically includes coverage for the building itself (dwelling coverage), protecting against risks like fire, storms, vandalism, and certain types of water damage.
What is not usually covered by building insurance?
- Damage to personal belongings: Building insurance does not cover personal items like furniture, electronics, or clothing. For these, a separate contents insurance policy is usually required.
- Wear and tear: Gradual deterioration of the building due to age or normal use (such as broken tiles or worn-out pipes) is typically not covered.
- Flood damage: Standard building insurance might not cover flooding unless specifically included in the policy. Separate flood insurance may be needed in high-risk areas.
- Subsidence or ground movement: Damage caused by subsidence, landslides, or earth movement might not be included unless specifically stated in the policy.
- Negligence or intentional damage: Damage that occurs due to neglect or intentional actions, such as not maintaining the property or causing damage on purpose, is usually excluded.
At what point do you need buildings insurance?
- Property Ownership: If you own a building, whether residential or commercial, buildings insurance is highly recommended to cover potential damage from events like fire, flood, storms, vandalism, or accidents.
- Mortgage Requirement: Most mortgage lenders require you to have buildings insurance in place as part of the loan agreement, ensuring the property is covered in case of damage that could affect its value or the lender's investment.
- Renting Out Property: If you rent out property, buildings insurance is essential to cover the structure and any potential damage caused by tenants or external factors.
- New Purchases: If you buy a new home or property, buildings insurance should be arranged before you take possession to ensure the property is protected from day one.
- Significant Renovations: If you're carrying out major renovations or extensions on a property, you might need additional buildings insurance to cover the works and any risks associated with construction.
REQUEST A QUOTE
Speak with a CA Workers Compensation Insurance specialist today!
Learn More About Workers Comp. Insurance
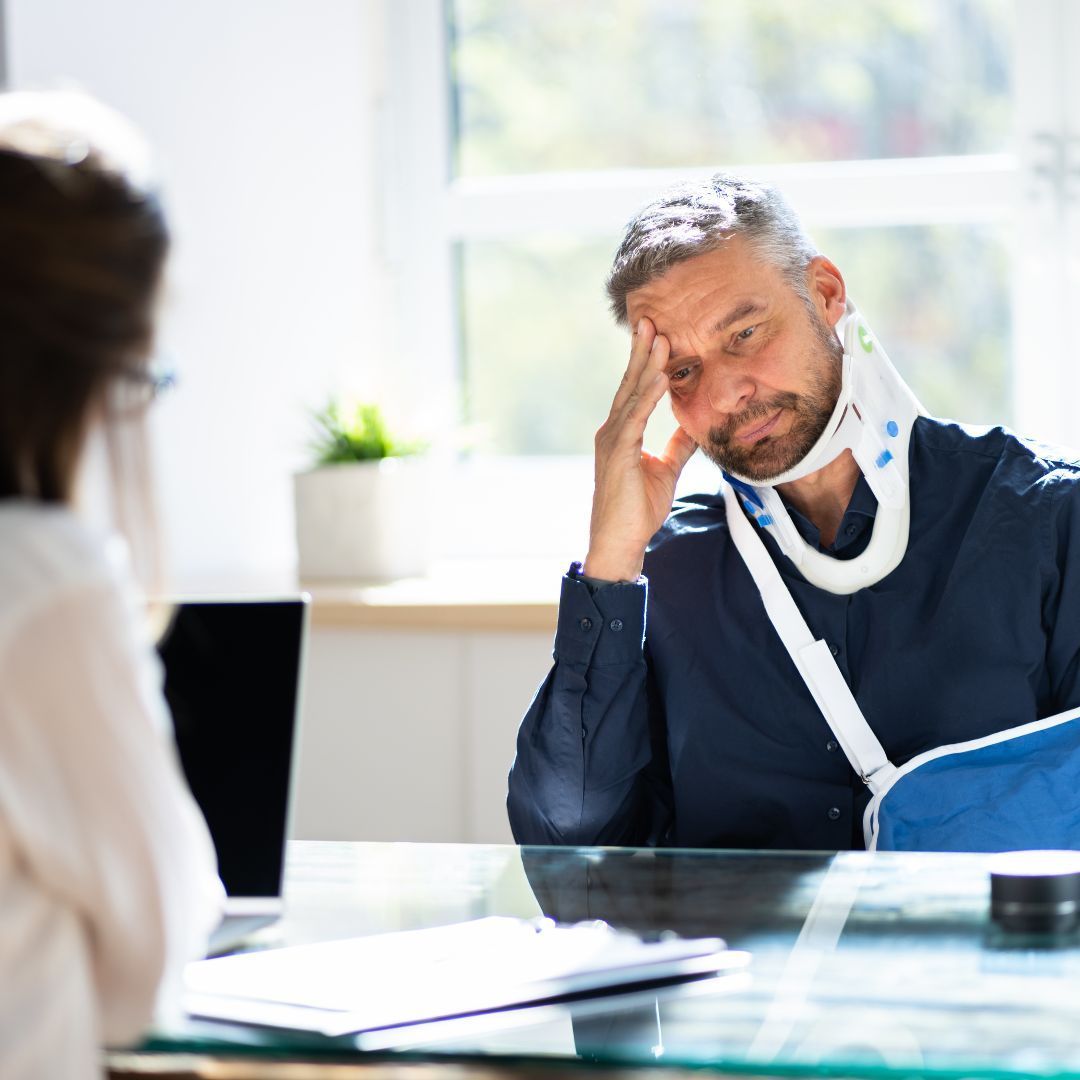
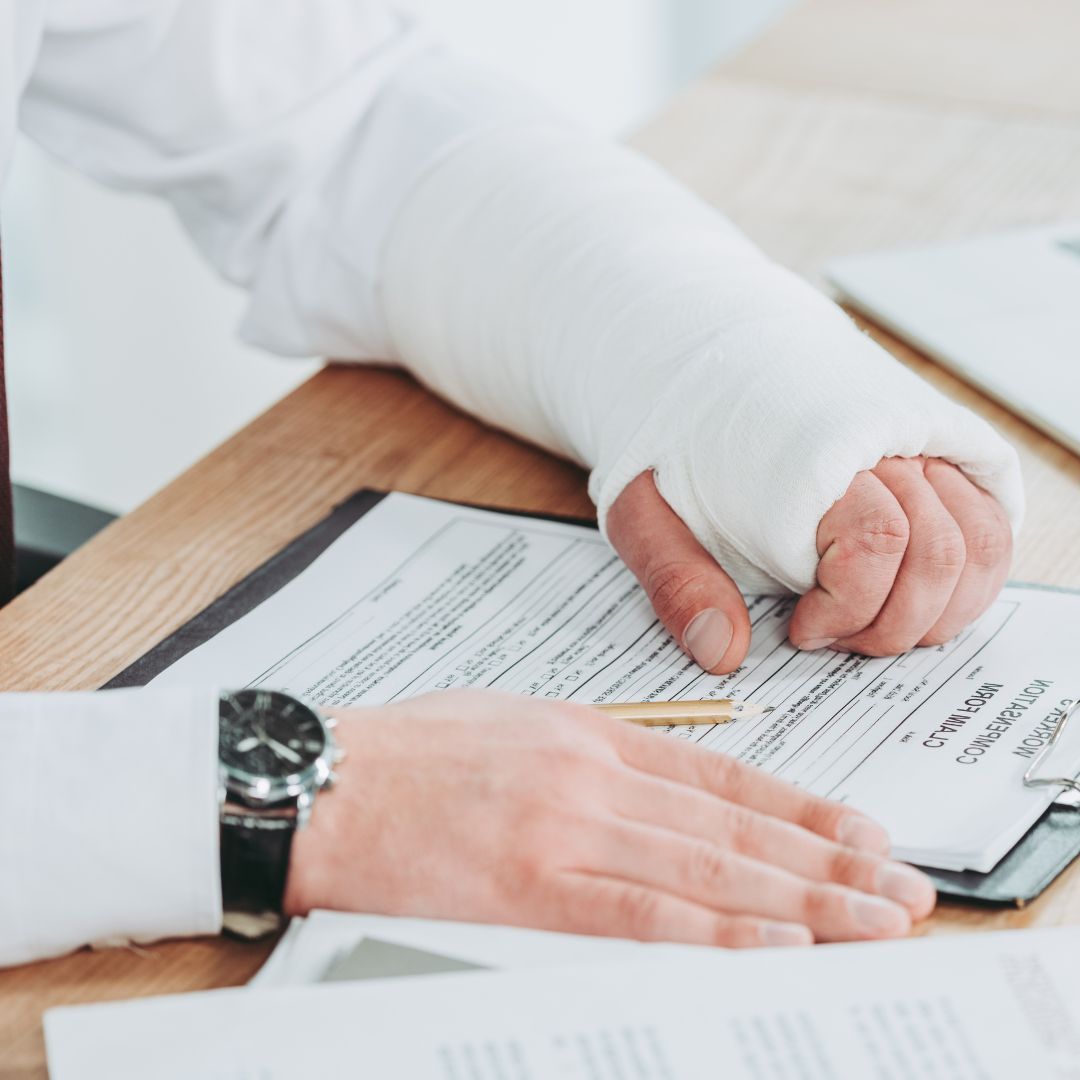