Workers Comp Insurance California For Machine Shops
Index
Understanding Workers' Comp Insurance
California's Workers' Comp Insurance Laws
How to Obtain Workers' Comp Insurance in California
Costs Associated with Workers' Comp Insurance
Filing a Workers' Comp Insurance Claim in California
Contact Us
Phone
886-226-4436
Location
9340 Bolsa Ave, Westminster, CA 92683
Workers Comp By City
Machine Shops: Your Ultimate Guide to Understanding Their Role and Importance
Machine shops are essential in modern manufacturing, serving as the backbone of industries that require precision-engineered components. These workshops utilize advanced machinery, tools, and skilled professionals to fabricate metal and plastic parts used in various sectors such as automotive, aerospace, medical, and electronics. The industry continues to evolve with advancements in automation, CNC technology, and material innovations that enhance efficiency and accuracy.
Why Machine Shops Are Essential
Machine shops play a crucial role in manufacturing and industrial production. Here’s why they are indispensable:
Precision and Customization
- Machine shops use high-precision tools like CNC (Computer Numerical Control) machines to create complex and detailed components.
- Custom machining allows manufacturers to tailor designs according to specific industrial requirements.
- Advanced software ensures minimal errors, improving the accuracy of the final product.
Cost-Effectiveness and Efficiency
- CNC machines and automated processes reduce labor costs and production time.
- Mass production of metal and plastic parts leads to lower per-unit costs.
- Machine shops enhance efficiency by minimizing material waste through optimized cutting and fabrication techniques.
Durability and Quality Assurance
- Precision machining ensures high-quality, durable components that meet industry standards.
- Regular inspections and testing ensure compliance with safety and performance regulations.
- Machined components provide superior strength and longevity compared to mass-produced alternatives.
Sustainability and Recycling Innovations
- Many machine shops recycle metal shavings and scrap to minimize waste.
- Energy-efficient machining processes contribute to sustainable manufacturing.
- The industry is increasingly incorporating biodegradable lubricants and coolants to reduce environmental impact.
Key Features of a Successful Machine Shop
A high-quality machine shop possesses distinct characteristics that ensure efficiency, precision, and sustainability. Here are some key features:
Advanced Machinery and Automation
- Utilization of CNC machines, milling machines, lathes, and EDM (Electrical Discharge Machining) equipment.
- Automated systems that enhance precision, reduce errors, and increase production speed.
- Robotics and AI-driven monitoring for quality control and operational efficiency.
Material Innovation and Sustainability Practices
- Usage of high-performance metals, alloys, and plastics tailored for industrial applications.
- Recycling initiatives that reduce material waste and enhance sustainability.
- Research and development efforts to introduce eco-friendly machining processes.
Stringent Quality Control Measures
- Adherence to industry standards such as ISO 9001 and AS9100 for aerospace components.
- In-house testing for tolerance, durability, and resistance.
- Routine inspections and certifications to maintain consistent product quality.
Skilled Workforce and Continuous Training
- Experienced machinists, engineers, and quality control experts.
- Regular training programs to stay updated with technological advancements.
- Safety protocols and workplace best practices to maintain operational excellence.
Types of Machining Processes
Different machining techniques cater to various industrial applications. Here are some of the most common methods:
CNC Machining
- One of the most widely used techniques for precision manufacturing.
- Utilizes computer-controlled cutting tools for accuracy and efficiency.
- Suitable for mass production and prototyping of intricate components.
Milling
- Involves the use of rotary cutters to remove material from a workpiece.
- Ideal for producing detailed parts with various shapes and sizes.
- CNC milling machines enable high-speed and precise cutting.
Turning (Lathe Machining)
- The process of rotating a workpiece while a cutting tool shapes it.
- Commonly used for cylindrical parts such as shafts and bearings.
- High-speed turning ensures smooth finishes and precise dimensions.
Grinding
- A finishing process that enhances surface smoothness and precision.
- Used to achieve tight tolerances and improve part aesthetics.
- Common in automotive, aerospace, and medical industries.
Electrical Discharge Machining (EDM)
- Uses electrical sparks to cut complex shapes from conductive materials.
- Suitable for creating fine details and intricate geometries.
- Ideal for hard metals that are difficult to machine with traditional methods.
Welding and Fabrication
- Involves joining metal components using heat or pressure.
- Essential for creating large-scale metal structures and assemblies.
- Advanced techniques like laser welding ensure precision and durability.
Common Applications of Machine Shops
Machine shops are integral to various industries, producing critical components for diverse applications. Here are some major sectors that rely on precision machining:
Automotive Industry
- Engine components, transmission parts, and suspension systems.
- Custom machining for high-performance and electric vehicles.
- Precision machining ensures fuel efficiency and durability.
Aerospace and Defense
- Aircraft engine parts, landing gear components, and turbine blades.
- High-tolerance machining ensures safety and performance.
- Military equipment and defense systems require robust machining solutions.
Medical Equipment Manufacturing
- Surgical instruments, implants, and prosthetics.
- Precision machining ensures biocompatibility and patient safety.
- Custom medical devices tailored to specific healthcare needs.
Electronics and Semiconductor Industry
- Micro-components for circuit boards and semiconductor devices.
- Heat sinks and enclosures for electronic systems.
- CNC machining ensures high accuracy for delicate components.
Construction and Heavy Equipment
- Structural components for buildings, bridges, and machinery.
- Precision-machined hydraulic parts for construction equipment.
- Heavy-duty machining ensures long-lasting performance in harsh environments.
Future Trends in Machine Shops
The machining industry continues to evolve with technological advancements and sustainability initiatives. Here are some key trends shaping the future:
Smart Manufacturing and Industry 4.0
- AI-driven quality control for defect detection and process optimization.
- IoT-enabled machines for real-time monitoring and predictive maintenance.
- Data analytics to improve efficiency and reduce downtime.
3D Printing and Additive Manufacturing
- Integration of 3D printing with CNC machining for rapid prototyping.
- Reduces material waste and allows for on-demand production.
- Expands possibilities for complex geometries and lightweight designs.
Sustainable Machining Practices
- Development of biodegradable coolants and lubricants.
- Emphasis on recycling and eco-friendly material sourcing.
- Energy-efficient CNC machines to minimize carbon footprint.
Automation and Robotics
- Increased use of robotic arms for high-speed precision machining.
- Reduction in manual labor and improved production consistency.
- Advanced automation improves safety and operational efficiency.
Key Aspects of Machine Shops
Machine shops are multifaceted operations that combine skilled labor, advanced machinery, and robust quality control processes to produce high-precision parts. Below are the primary considerations for any successful machine shop operation.
1. Machining Processes
- Milling:
One of the most common processes in machine shops, milling involves using rotating cutting tools to remove material from a workpiece. CNC (Computer Numerical Control) milling machines can create intricate shapes, pockets, and channels with high accuracy. - Turning (Lathe Work):
Turning is performed on lathes, where the workpiece rotates against a stationary cutting tool. This process is used to produce cylindrical or conical parts—such as shafts, rods, and threaded fasteners—often with tight dimensional tolerances. - Drilling:
Drilling is a fundamental operation for creating holes in a workpiece. It’s commonly done with drill presses or CNC machines, offering precise hole placement in everything from small components to large fabrications. - Grinding:
Grinding uses an abrasive wheel to achieve high-precision finishes and tight tolerances. It is particularly useful for refining surfaces or making precision cuts in hardened materials. - EDM (Electrical Discharge Machining):
EDM employs electrical discharges (sparks) to erode conductive materials. This process is suitable for hard metals and complex shapes, where traditional machining may struggle. - Welding and Fabrication:
Many machine shops also integrate welding, metal forming, and fabrication into their offerings, enabling them to produce complete assemblies in-house.
2. Material Selection
Like any manufacturing facility, machine shops must consider the properties of raw materials to match project requirements. Commonly used materials include:
- Steel: A go-to metal for its strength, durability, and versatility. Used for automotive parts, tooling, and machinery components.
- Aluminum: Known for its lightweight properties, excellent corrosion resistance, and good machinability—ideal for aerospace, automotive, and consumer electronics.
- Stainless Steel: Offers high corrosion resistance, making it suitable for food processing, medical equipment, and marine applications.
- Titanium: Valued for its high strength-to-weight ratio and corrosion resistance, making it essential for aerospace, military, and biomedical components.
- Brass and Copper Alloys: Frequently used in electrical components, plumbing fixtures, and decorative applications due to their conductive properties and aesthetic appeal.
- Plastics and Composites: Though metals are dominant, many machine shops also process plastics (like nylon, ABS, or PEEK) and composite materials to meet specific industry needs.
3. Quality Control
Quality assurance is paramount in machine shops, given that many industries rely on precision parts to ensure safety and performance. Quality control measures typically include:
- Dimensional Inspections: Using calipers, micrometers, and coordinate measuring machines (CMMs) to verify part dimensions.
- Surface Finish Evaluation: Ensuring the surface roughness meets the functional and aesthetic standards of the finished product.
- Material Testing: Confirming material composition and mechanical properties match client specifications.
- Process Validation: Regularly calibrating machines and tools, maintaining consistent machining parameters, and documenting production runs.
- Compliance with Standards: Machine shops often adhere to certifications like ISO 9001, AS9100 (aerospace), or TS 16949 (automotive) to meet strict industry requirements.
Importance of Machine Shops
Machine shops are indispensable to the modern manufacturing landscape for several reasons:
- Precision Manufacturing:
Many industries require components with tolerances in the thousandths of an inch. Machine shops excel at achieving these levels of precision. - Customization and Flexibility:
From small-batch prototypes to large-scale production runs, machine shops adapt to varying product demands and design iterations. - Innovation and Product Development:
By working closely with design engineers, machine shops drive innovation, creating new parts, improving existing designs, and rapidly testing prototypes. - Cost-Effective Solutions:
Skilled machinists and efficient processes help reduce material waste and rework, leading to lower overall manufacturing costs. - Critical Support for Other Industries:
Machine shops bolster sectors like aerospace, automotive, and healthcare, producing everything from airplane components to surgical instruments.
Key Features of a Well-Functioning Machine Shop
A successful machine shop balances efficiency, accuracy, and sustainability. Here are the hallmarks of a well-optimized operation:
- Modern Machinery:
Investing in advanced CNC machines, high-speed cutting tools, and automated equipment ensures faster production and consistent results. - Skilled Workforce:
Trained machinists, engineers, and quality control specialists are crucial. Continuous staff development through apprenticeships, certifications, and on-the-job training keeps the shop competitive. - Efficient Workflow Layout:
Thoughtful organization of equipment and materials reduces setup times and minimizes unnecessary movement, directly impacting production speed. - Safety and Compliance:
Machine shops must adhere to workplace safety standards, ensuring employees use protective gear, follow proper machine handling protocols, and maintain a clean environment. - Maintenance Strategy:
Regular upkeep and inspection of machinery prevent breakdowns, reduce downtime, and guarantee product consistency. - Data-Driven Monitoring:
Using sensors and software to track machine performance and production metrics allows shops to identify inefficiencies and optimize processes in real-time.
Why Machine Shops Are Essential for Sustainable Development
While sustainability might not be the first concept associated with machine shops, their impact on eco-friendly initiatives is significant:
- Reducing Waste through Precision:
By machining parts accurately, shops minimize raw material usage. The precision reduces scrap rates, leading to less overall waste. - Energy Efficiency:
Modern CNC machines and production techniques often use less energy than older mechanical setups. Continuous improvements in tooling and coolant systems further enhance energy savings. - Prolonging Product Lifecycles:
Quality machining ensures parts and products last longer, reducing the need for frequent replacements and conserving resources. - Collaboration with Green Industries:
Machine shops play a role in manufacturing components for renewable energy systems, electric vehicles, and sustainable infrastructure projects. - Recycling and Reusing Materials:
Metal chips and offcuts can be collected and recycled. Many shops also invest in systems to reclaim coolants and lubricants, further cutting down on environmental impact.
Challenges Facing Machine Shops
Like any manufacturing sector, machine shops encounter several issues that can hinder their growth and performance:
- Skilled Labor Shortage:
As older machinists retire, finding new talent with the right technical and analytical skills becomes more difficult. - Increasing Costs:
Raw material prices, energy expenses, and equipment investments can fluctuate, affecting profit margins and project feasibility. - Technological Complexity:
Rapid advancements in CNC programming, automation, and additive manufacturing require continuous education and upgrades. - Supply Chain Disruptions:
Global economic changes or geopolitical events can slow the flow of essential materials or cause cost spikes. - Regulatory Compliance:
Machine shops serving industries with stringent standards—like medical or aerospace—must continuously adapt to evolving regulations, which can be resource-intensive.
How to Improve Machine Shop Efficiency
Addressing the challenges above often involves strategic investments, policy updates, and cultural shifts within the organization:
- Automation and Robotics:
Introducing robotic arms or automated part loaders can handle repetitive tasks, freeing skilled machinists for more complex work. - Lean Manufacturing Principles:
Reducing waste, streamlining workflows, and optimizing production schedules can cut costs and improve overall output. - Data Analytics and AI:
Software-driven solutions can monitor machine performance in real-time, predict maintenance needs, and optimize tool usage, significantly reducing downtime. - Ongoing Training and Development:
Investing in apprenticeships, certifications, and continuing education for staff ensures that the workforce remains highly skilled and adaptable. - Collaboration and Knowledge Sharing:
Networking with industry peers, joining trade associations, and attending conferences help machine shops stay up-to-date on best practices and technology trends.
Investment Opportunities in Machine Shops
For entrepreneurs, investors, or existing manufacturers, there are various ways to capitalize on the demand for precision machining:
- Niche Specialization:
Focusing on a particular industry—such as medical devices, aerospace components, or aftermarket automotive parts—can yield higher profit margins due to specialized expertise. - Automation and Smart Factories:
Investing in state-of-the-art CNC machines, robotics, and data-driven systems can set a shop apart, enabling higher production volumes with lower labor costs. - Additive Manufacturing Integration:
Combining traditional machining with 3D printing allows shops to offer hybrid solutions, handle complex geometries, and speed up prototyping. - Green Manufacturing:
Embracing sustainable practices—from solar panel installations to recycling programs—attracts environmentally conscious clients and can lead to government incentives. - Global Supply Chains:
Leveraging international partnerships to source raw materials or distribute finished goods can expand a machine shop’s reach and diversify revenue streams.
Future Trends in Machine Shops
Machine shops are at the forefront of technological progress, poised to evolve as new methods and market demands emerge:
- Hybrid Manufacturing:
Shops that merge additive (3D printing) and subtractive (milling, turning) processes will offer unique solutions for complex designs. - Smart Machining and IoT:
Internet of Things (IoT) sensors on machines can provide real-time data on wear, temperature, and vibration, enabling predictive maintenance and uninterrupted production. - Micro Machining and Nanotechnology:
As products become more compact, machine shops will push the boundaries of precision, working at microscopic scales to deliver ultra-fine details. - Artificial Intelligence (AI) Optimization:
AI-powered tools will refine CNC code automatically, optimizing cutting paths and tool usage for maximum efficiency and minimal waste. - Sustainable Materials and Practices:
Demand for eco-friendly manufacturing will rise, spurring further adoption of recycled metals, biodegradable coolants, and energy-efficient systems. - Reshoring and Local Manufacturing:
Fluctuating global markets may drive some companies to move production back to local machine shops, leading to increased domestic demand for precision manufacturing services.
Understanding Machine Shops
A machine shop is a facility where raw materials—commonly metals, plastics, and composites—are cut, shaped, and formed into finished or semi-finished parts. These shops can range from small-scale workshops focusing on niche projects to large industrial operations equipped with advanced automated systems. They play a pivotal role in numerous sectors, including automotive, aerospace, defense, medical, electronics, and construction.
Key objectives in machine shop operations include:
- Precision: Maintaining tight tolerances and high quality.
- Efficiency: Reducing production time and minimizing waste.
- Cost-Effectiveness: Balancing overhead costs with profit margins.
- Safety: Ensuring a safe working environment for operators and staff.
Today’s machine shops must adapt to rapidly changing technologies and market demands. Computer Numerical Control (CNC) machines, robotics, and Industry 4.0 innovations have transformed traditional machining, driving higher accuracy and productivity. As these advancements continue, modern machine shops must stay agile and adopt evolving processes to remain competitive.
Key Aspects of Machine Shops
Machine shops are complex environments that demand a thorough understanding of tools, materials, safety standards, and production methods. Several critical factors influence their efficiency, output, and profitability:
- Machinery and Equipment
- CNC Machines: High-precision tools such as CNC lathes, milling machines, and routers.
- Manual Equipment: Conventional lathes, drill presses, and milling machines, often used for small-scale or custom jobs.
- Supporting Tools: Grinders, saws, tapping machines, and inspection devices.
- Material Selection
- Metals: Steel, aluminum, brass, and titanium for strength and durability.
- Plastics and Composites: Lightweight options often used in aerospace, automotive, and medical applications.
- Exotic Alloys: Specialty materials designed for high-temperature or corrosive environments.
- Workforce Expertise
- Skilled Operators: Machinists, CNC programmers, and inspectors.
- Technical Leadership: Engineers and project managers coordinating design, fabrication, and assembly.
- Training and Certification: Continuous skill development ensures quality and adherence to industry standards.
- Quality Control
- Metrology and Inspection: Using devices like coordinate measuring machines (CMMs) for dimensional checks.
- Standards Compliance: Meeting ISO, AS9100 (aerospace), or other sector-specific certifications.
- Documentation: Maintaining detailed inspection reports and traceability records.
- Operational Efficiency
- Lean Manufacturing: Methods to minimize waste and streamline processes.
- Automation: Robots and automated systems for repetitive or complex tasks.
- Inventory Management: Effective supply chain coordination to avoid material shortages or overstock.
Importance of Machine Shops in Society
Machine shops are at the forefront of industrial innovation, providing components and assemblies essential to everyday products and specialized applications alike. Their importance extends beyond manufacturing lines, influencing economic growth, national security, and technological advancements.
Key Benefits of Machine Shops:
- Innovation and Customization:
- Ability to produce prototypes and specialized parts for research, development, and custom applications.
- Economic Growth:
- Job creation for skilled labor, engineers, and technicians.
- Contribution to local and global supply chains.
- Infrastructure Support:
- Production of critical components for transportation networks, power generation, and communications.
- Maintenance and repair of industrial machinery to reduce downtime.
- Defense and Security:
- Manufacturing of military-grade equipment and aerospace components.
- Precision engineering for defense applications ensures reliability and safety.
- Medical Advancements:
- Machined parts for diagnostic devices, implants, and surgical tools.
- Ensuring strict compliance with regulatory standards for patient safety.
In essence, machine shops enable countless industries to function smoothly. From constructing bridges and airplanes to fabricating medical instruments, these facilities form the bedrock of industrial progress.
Types of Machine Shops
Machine shops can be classified based on the services they provide, the industries they serve, and the equipment they utilize. Understanding these distinctions helps businesses and clients select the most suitable partner for their needs.
- General Job Shops
- Handle diverse projects for multiple industries.
- Typically equipped with both CNC and manual machines for high versatility.
- Prototype Shops
- Specialize in creating low-volume, high-precision prototypes.
- Work closely with product development teams and inventors.
- Production Shops
- Focus on large-scale manufacturing runs.
- Employ advanced automation and high-speed machining to meet mass production demands.
- Specialty or Niche Shops
- Cater to specific sectors like aerospace, automotive, or medical.
- Invest in specialized equipment and certifications pertinent to their niche.
- Maintenance and Repair Operations (MRO)
- Provide repair, refurbishment, and retrofitting services for industrial machinery.
- Essential for companies seeking to extend equipment lifespan and reduce downtime.
Machine Shop Processes
Just as plastic product manufacturers employ techniques like injection molding or extrusion, machine shops rely on an array of processes to shape and refine materials. Each method has its advantages and is chosen based on factors like material properties, desired precision, and production volume.
- Turning (Lathe Operations)
- Rotating the workpiece against a stationary cutting tool.
- Ideal for creating cylindrical parts such as shafts, rods, and bushings.
- Can achieve tight tolerances and smooth finishes.
- Milling
- Rotating cutting tools remove material from a stationary workpiece.
- Produces complex shapes, slots, and holes.
- CNC milling machines offer high precision and repeatability.
- Drilling and Tapping
- Creating holes and threads in a workpiece.
- Essential for assemblies requiring fasteners.
- Grinding
- Abrasive wheels remove fine layers of material for surface finishing.
- Achieves extremely tight tolerances and superior surface quality.
- EDM (Electrical Discharge Machining)
- Uses electrical sparks to erode conductive materials in a controlled manner.
- Ideal for intricate shapes and hard-to-machine metals.
- CNC and Automation
- Computer-controlled systems for high-precision, repeatable production.
- Reduced human error and improved efficiency.
- Integrated software enables complex geometries and rapid setup changes.
- Inspection and Quality Assurance
- Coordinate measuring machines (CMMs) and optical systems verify dimensional accuracy.
- Statistical Process Control (SPC) techniques monitor production consistency.
Industry Governance and Regulations
Machine shops must adhere to various regulations and standards to ensure product safety, quality, and worker well-being. These measures protect both employees and end-users, fostering trust in the manufacturing process.
- Occupational Safety and Health Administration (OSHA)
- Sets guidelines for workplace safety and hazard control.
- Regular audits and inspections to ensure compliance.
- International Standards Organization (ISO)
- ISO 9001 for quality management, ISO 14001 for environmental management, among others.
- Demonstrates a commitment to consistent quality and continuous improvement.
- Sector-Specific Standards
- Aerospace (AS9100): Emphasizes traceability and risk management.
- Automotive (IATF 16949): Focuses on defect prevention and continuous improvement.
- Environmental Regulations
- Governing waste disposal, emissions control, and energy consumption.
- Encouraging sustainable practices and the use of eco-friendly coolants or lubricants.
- Trade and Industry Associations
- Organizations like the National Tooling and Machining Association (NTMA) advocate for machinists.
- Provide resources on best practices, lobbying efforts, and professional development.
Compliance with these standards not only ensures the safety of workers and consumers but also fortifies a shop’s reputation for reliability and excellence.
Challenges in Machine Shop Operations
Despite their critical role in manufacturing, machine shops face a host of challenges—both longstanding and emerging. Addressing these obstacles is key to maintaining a competitive edge.
- Skilled Labor Shortage
- The retirement of experienced machinists outpaces new entrants into the field.
- Hiring and retaining qualified CNC programmers and operators becomes increasingly difficult.
- Technological Upgrades
- Rapid advancements in automation and digitalization demand ongoing capital investments.
- Integrating Industry 4.0 concepts requires staff training and robust IT support.
- Global Competition
- Low-cost producers in regions with cheaper labor can undercut pricing.
- Necessitates a focus on high-quality, value-added services to remain competitive.
- Supply Chain Volatility
- Fluctuations in raw material availability and prices affect operational costs.
- Logistical disruptions impact lead times and inventory management.
- Regulatory Compliance
- Evolving standards mandate continuous updates to processes and documentation.
- Non-compliance risks fines, reputational damage, and loss of business.
- Environmental and Sustainability Concerns
- Pressure to reduce waste, energy consumption, and use of hazardous substances.
- Growing importance of eco-friendly solutions and responsible manufacturing practices.
Investment Opportunities in Machine Shops
The machine shop sector presents diverse investment avenues, ranging from new technologies to specialized services and sustainable innovations. Strategic investments can drive growth, improve profitability, and ensure long-term competitiveness.
- Advanced CNC and Automation
- High-speed milling and multi-axis turning centers for complex geometries.
- Robotic handling systems to boost production rates and lower labor costs.
- Industry 4.0 and Digitalization
- Smart sensors and IoT (Internet of Things) for real-time machine monitoring.
- Data analytics to optimize workflows, predict maintenance needs, and reduce downtime.
- Additive Manufacturing (3D Printing)
- Hybrid setups combining traditional machining with metal 3D printing.
- Prototyping and low-volume production with minimal material waste.
- Training and Workforce Development
- Building partnerships with technical schools and apprenticeship programs.
- Upskilling existing staff for new technologies, ensuring retention and loyalty.
- Sustainability and Green Initiatives
- Investing in energy-efficient equipment and processes.
- Recycling and responsible waste management to meet environmental regulations.
Future Trends in Machine Shops
As technology evolves and industries demand more specialized products, machine shops are on the cusp of significant transformation. Several emerging trends promise to redefine how these facilities operate and compete on the global stage.
- Increased Automation and Robotics
- Robots handling repetitive tasks, freeing skilled machinists for intricate work.
- Collaborative robots (cobots) working alongside human operators for safer, more efficient operations.
- AI-Driven Manufacturing
- Machine learning algorithms optimizing cutting parameters, tool paths, and machine utilization.
- Predictive maintenance reducing downtime by identifying issues before they escalate.
- Advanced Materials and Processes
- Growing use of composite materials, titanium alloys, and superalloys in aerospace and medical industries.
- Continuous improvement in machining methods for higher accuracy and reduced cycle times.
- Localized Production and On-Demand Manufacturing
- Shortening supply chains with local machine shops supporting regional markets.
- Customizable and flexible production runs catering to fast-changing consumer demands.
- Sustainable Machining
- Emphasis on green manufacturing techniques—dry machining or minimal lubrication to reduce coolant waste.
- Implementation of renewable energy sources and recycling programs.
- Global Collaboration and Standards
- International trade agreements shaping access to raw materials and new markets.
- Harmonized standards for quality, safety, and environmental impact, easing cross-border collaboration.
Machine Shops: A Comprehensive Guide to Understanding Their Role and Function
Machine shops play a critical role in the manufacturing and engineering industries by providing precision machining services that shape raw materials into functional parts. Whether you are looking to understand the processes, significance, or technological advancements shaping modern machining, this guide offers an in-depth insight into the machine shop industry.
What Is a Machine Shop?
A machine shop is a facility equipped with various tools and machinery used to fabricate metal and other materials into specific parts or components. These shops range from small-scale operations to large industrial setups that serve sectors like aerospace, automotive, construction, and medical device manufacturing. Machine shops employ advanced machining techniques, including milling, turning, grinding, and electrical discharge machining (EDM), to achieve precise specifications.
Why Machine Shops Are Essential
Machine shops are integral to the global economy, supporting innovation and production across numerous industries. The importance of machine shops is underscored by several key aspects:
Precision Manufacturing
- Machine shops provide high-precision components that meet stringent industry standards.
- Advanced CNC (Computer Numerical Control) machining allows for complex geometries and tight tolerances.
Economic Contribution
- The machining industry supports millions of jobs worldwide, from machinists and engineers to quality control specialists.
- It drives advancements in sectors such as automotive, medical, and defense industries.
Innovation and Customization
- Custom machine shops cater to specialized needs by producing prototypes and low-volume parts.
- Machining technology continually evolves, incorporating AI, automation, and robotics to enhance efficiency.
Key Components of a Successful Machine Shop
Strategic Planning
A machine shop must have a well-defined strategy, including:
- Material Selection: Choosing suitable materials, such as steel, aluminum, titanium, or composites, based on application needs.
- Process Optimization: Utilizing lean manufacturing techniques and automation to improve efficiency and reduce waste.
- Investment in Technology: Adopting CNC machines, 3D printing, and IoT-enabled monitoring systems.
Advanced Machining Techniques
Machine shops utilize various processes, including:
- CNC Milling: Cutting and shaping materials using rotary tools.
- CNC Turning: Producing cylindrical parts through lathes.
- Grinding and Finishing: Ensuring precise surface finishes and tolerances.
- Electrical Discharge Machining (EDM): A non-traditional process for intricate cuts in hard materials.
Strong Governance and Quality Assurance
- Regulatory Compliance: Adhering to industry standards such as ISO 9001 and AS9100 for aerospace machining.
- Quality Control Measures: Implementing rigorous inspection techniques, including CMM (Coordinate Measuring Machines) and laser scanning.
- Skilled Workforce: Continuous training and development of machinists and engineers to keep pace with technological advancements.
Challenges Faced by Machine Shops
Material Costs and Supply Chain Issues
- Fluctuations in raw material prices can affect production costs and profitability.
- Dependence on global supply chains for specialized metals and alloys.
Labor Shortages and Skill Gaps
- The machining industry faces a shortage of skilled workers due to the retirement of experienced machinists.
- Investments in vocational training and apprenticeship programs are essential.
Technological Advancements and Automation
- Small and mid-sized machine shops struggle to adopt expensive automation solutions.
- The transition to smart factories requires substantial investment in AI-driven manufacturing and IoT integration.
The Role of Private Entities in Machine Shop Development
Public-Private Partnerships (PPPs)
- Collaborations between government agencies and machine shops to develop advanced manufacturing capabilities.
- Investment in research and development (R&D) for next-generation machining technologies.
Corporate Social Responsibility (CSR)
- Companies investing in sustainable machining practices to reduce waste and energy consumption.
- Adoption of eco-friendly coolants and recycling programs for metal scraps.
Technological Innovation
- Use of smart sensors and real-time data analytics to optimize machining operations.
- Implementation of blockchain for secure and transparent supply chain management.
Benefits of a Well-Managed Machine Shop Industry
Product Quality and Customization
- Machine shops enable precision engineering with high-quality standards.
- Custom machining services allow for the creation of specialized parts in various industries.
Economic Growth and Job Creation
- The machine shop sector supports industrial growth and contributes to national GDP.
- Skilled machinists and engineers find rewarding career opportunities in high-tech manufacturing.
Sustainability and Environmental Efforts
- Implementation of green machining techniques to reduce energy consumption and waste.
- Development of recyclable metal alloys to promote circular economy principles.
Future Trends in Machine Shops
Smart Factories and Digital Transformation
- Adoption of AI and machine learning for predictive maintenance and quality control.
- IoT-enabled CNC machines for real-time monitoring and optimization.
Sustainable Material Usage
- Growth in eco-friendly and lightweight materials to reduce environmental impact.
- Research into biodegradable and composite materials for aerospace and medical applications.
Increased Collaboration and Policy Support
- Stronger alliances between manufacturers, policymakers, and educational institutions to bridge the skill gap.
- Government incentives for machine shops investing in automation and sustainable practices.
How much is insurance for a machine shop?
- Size of the shop: Larger machine shops with more employees or equipment will generally pay higher premiums.
- Location: Insurance costs can be influenced by the region or country where the machine shop is located, as risk factors like weather conditions, crime rates, or natural disasters can impact premiums.
- Type of coverage: Different types of insurance coverage are available, such as general liability, property insurance, workers' compensation, equipment breakdown insurance, and product liability. The more comprehensive the coverage, the higher the cost.
- Claims history: If the machine shop has a history of insurance claims, premiums could be higher.
- Employee count and payroll: More employees or higher payroll can increase workers' compensation insurance costs.
What is machinery insurance policy?
- Accidental Damage: If the machinery breaks down or gets damaged due to an unexpected event like a power surge, accident, or natural disaster, the policy helps cover the repair or replacement costs.
- Mechanical and Electrical Breakdown: If the machinery suffers from a mechanical or electrical failure that is not due to wear and tear, the insurance can cover the repair expenses.
- Theft or Vandalism: If the machinery is stolen or vandalized, this insurance will help the business recover its losses.
- Fire and Natural Disasters: If the machinery is damaged due to fire, flooding, or other natural calamities, the policy covers the replacement or repair.
- Third-Party Liability: Some policies may include coverage for damages caused by machinery to third parties or their property.
Is workers' compensation insurance mandatory for machine shops in California?
Yes, California law mandates that all businesses with employees carry workers' compensation insurance. This coverage provides benefits to employees who suffer work-related injuries or illnesses, covering medical expenses and lost wages.
Are there specific insurance requirements for machine shops in California?
Yes, California has specific regulations that machine shop owners must follow. It's essential to consult with an experienced insurance agent familiar with California's laws to determine the exact insurance requirements for your business.
REQUEST A QUOTE
Speak with a CA Workers Compensation Insurance specialist today!
Learn More About Workers Comp. Insurance
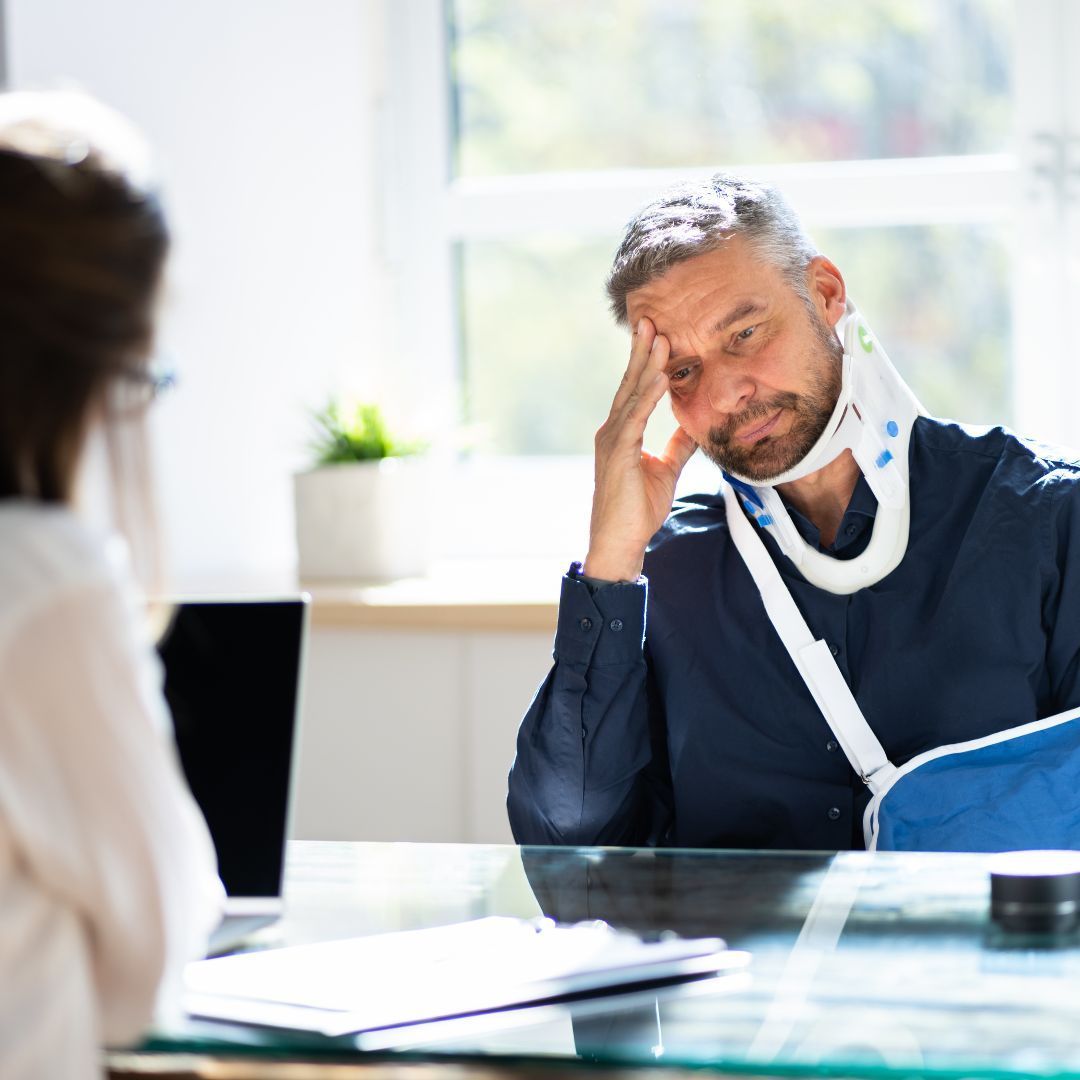
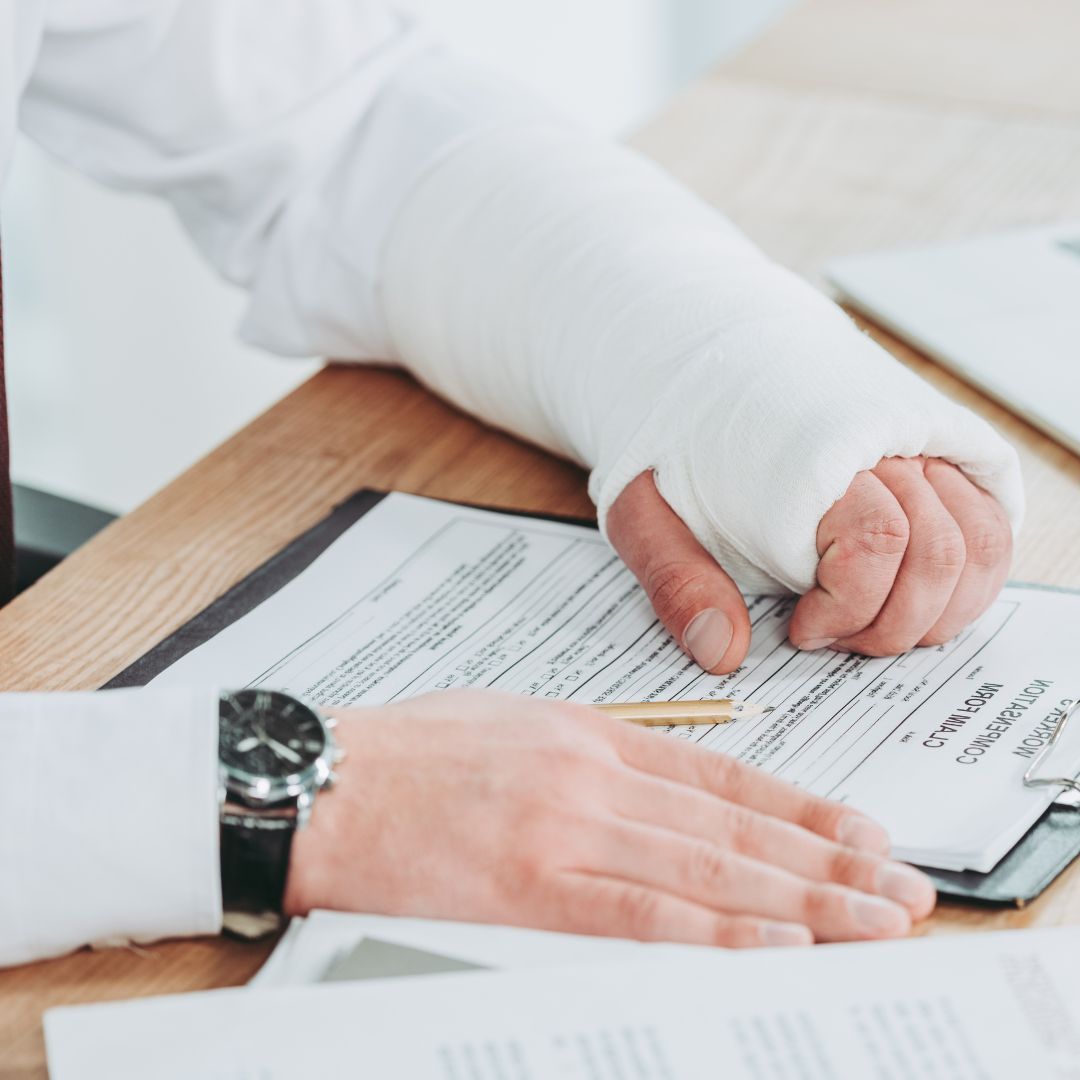