Workers Comp Insurance California For Plastic Product Manufacturing
Index
Understanding Workers' Comp Insurance
California's Workers' Comp Insurance Laws
How to Obtain Workers' Comp Insurance in California
Costs Associated with Workers' Comp Insurance
Filing a Workers' Comp Insurance Claim in California
Contact Us
Phone
886-226-4436
Location
9340 Bolsa Ave, Westminster, CA 92683
Workers Comp By City
Plastic Product Manufacturing: Your Ultimate Guide to Understanding Its Role and Importance
Plastic product manufacturing is a crucial industry that impacts almost every aspect of modern life. From packaging and consumer goods to medical equipment and automotive components, plastic manufacturing plays a vital role in various sectors. The industry is driven by innovation, sustainability efforts, and advanced production techniques that ensure efficiency and cost-effectiveness.
Why Plastic Product Manufacturing Is Essential
Plastic products serve a wide range of functions, making them indispensable in everyday life. Here’s why the plastic manufacturing industry is crucial:
Versatility and Customization
- Plastic materials can be molded into a variety of shapes, sizes, and textures.
- Manufacturers can tailor plastic properties to specific applications, including flexibility, durability, and resistance.
- Plastics can replace heavier materials like metal and glass, reducing overall production and transportation costs.
Cost-Effectiveness and Efficiency
- The mass production of plastic products is highly efficient, lowering manufacturing costs.
- Plastic materials require less energy to produce compared to metals and glass.
- Advances in automation and injection molding have streamlined production, reducing labor costs and improving output.
Durability and Longevity
- Many plastics are resistant to corrosion, chemicals, and environmental degradation.
- Plastic products have a long lifespan, reducing the need for frequent replacements.
- Enhanced material properties contribute to safety and reliability in industries like healthcare and automotive.
Sustainability and Recycling Innovations
- The industry is shifting towards biodegradable and recyclable plastics.
- Many manufacturers are adopting eco-friendly practices, such as using post-consumer recycled plastics.
- Innovations in bio-based plastics aim to reduce reliance on fossil fuels.
Key Features of a Successful Plastic Product Manufacturing Facility
A high-quality plastic manufacturing operation possesses distinct characteristics that ensure efficiency and sustainability. Here are some key features:
Advanced Machinery and Automation
- State-of-the-art injection molding machines, extrusion equipment, and blow molding technology.
- Automated systems that enhance precision, reduce waste, and improve production speed.
- Robotics and AI-driven monitoring for quality control and efficiency.
Material Innovation and Sustainability Practices
- Use of biodegradable, recyclable, and bio-based plastics to reduce environmental impact.
- Efficient waste management and recycling initiatives within the production process.
- Research and development efforts to improve material properties and eco-friendliness.
Stringent Quality Control Measures
- Strict adherence to industry standards and safety regulations.
- In-house testing for durability, resistance, and compliance with environmental norms.
- Regular inspections and certifications to ensure consistency in product quality.
Skilled Workforce and Continuous Training
- A team of trained engineers, technicians, and quality control experts.
- Ongoing training programs to keep up with technological advancements.
- Safety protocols and workplace best practices to ensure operational efficiency.
Types of Plastic Product Manufacturing Processes
Different manufacturing processes cater to various plastic applications. Here are some common methods:
Injection Molding
- One of the most widely used techniques in plastic manufacturing.
- Molten plastic is injected into a mold cavity, cooled, and solidified.
- Suitable for high-volume production of complex and precise components.
Blow Molding
- Used to create hollow plastic products such as bottles and containers.
- Air pressure is applied to expand molten plastic inside a mold.
- Ideal for lightweight and uniform-thickness products.
Extrusion Molding
- Involves pushing molten plastic through a shaped die to create continuous profiles.
- Commonly used for pipes, tubing, sheets, and window frames.
- Efficient and cost-effective for large-scale production.
Rotational Molding
- Used for producing large, hollow, and seamless plastic products like tanks and playground equipment.
- Plastic powder is heated and rotated within a mold to coat the interior evenly.
- Ensures high durability and uniform thickness.
Thermoforming
- Involves heating a plastic sheet and molding it into a specific shape using a mold.
- Often used for packaging, trays, and disposable products.
- Allows for cost-effective production of lightweight products.
Common Applications of Plastic Product Manufacturing
Plastic products are present in almost every industry. Here are some major applications:
Packaging Industry
- Food and beverage containers, bottles, and wrappers.
- Pharmaceutical and medical packaging to maintain hygiene and safety.
- Durable and lightweight packaging solutions for logistics and transportation.
Automotive Industry
- Dashboard components, bumpers, and fuel tanks.
- Lightweight plastic materials help improve fuel efficiency.
- Safety features such as airbags and seat belt components.
Healthcare and Medical Devices
- Disposable syringes, IV bags, and surgical instruments.
- Sterile and durable plastic components used in medical equipment.
- Biocompatible materials for implants and prosthetics.
Electronics and Consumer Goods
- Mobile phone cases, computer components, and wiring insulation.
- Durable plastic materials provide insulation and protection for electrical applications.
- Lightweight and ergonomic designs for home appliances and gadgets.
Construction and Infrastructure
- Plastic pipes, insulation materials, and roofing solutions.
- Weather-resistant plastic products for long-lasting construction elements.
- Sustainable alternatives like recycled plastic bricks and panels.
Furniture and Household Items
- Chairs, tables, storage bins, and decorative items.
- Affordable and lightweight materials with aesthetic appeal.
- UV-resistant plastics for outdoor furniture durability.
Future Trends in Plastic Product Manufacturing
The plastic manufacturing industry continues to evolve with advancements in technology and sustainability. Here are some key trends shaping the future:
Biodegradable and Eco-Friendly Plastics
- Increased research into bio-based polymers made from renewable sources like corn and sugarcane.
- Development of compostable plastics to reduce environmental pollution.
- Integration of plant-based materials to create sustainable alternatives.
3D Printing and Customization
- Additive manufacturing allows for rapid prototyping and customized plastic products.
- Reduces material waste and enables on-demand production.
- Expands possibilities for intricate designs and innovative applications.
Circular Economy and Recycling Innovations
- Emphasis on closed-loop recycling systems to reduce plastic waste.
- Advanced sorting and processing technologies for efficient material reuse.
- Corporate responsibility initiatives promoting sustainable plastic use.
Smart and Functional Plastics
- Integration of nanotechnology for self-healing and antimicrobial properties.
- Smart packaging solutions with embedded sensors for freshness tracking.
- Conductive plastics for flexible electronics and wearable technology.
Automation and Industry 4.0 Integration
- AI-driven quality control for defect detection and process optimization.
- Robotic automation to improve efficiency and reduce manual labor.
- Data analytics and IoT-enabled systems for real-time monitoring and decision-making.
Understanding Plastic Product Manufacturing
Plastic product manufacturing is a crucial industry that involves the design, production, and distribution of plastic goods used in various sectors, including packaging, automotive, construction, and healthcare. The process of plastic manufacturing encompasses multiple techniques such as injection molding, extrusion, and blow molding, each catering to different product requirements.
Key Aspects of Plastic Product Manufacturing
Manufacturing Processes
Plastic manufacturing employs various techniques, each suited to specific applications:
- Injection Molding: Common for mass-producing items like bottle caps and containers.
- Blow Molding: Used for making hollow plastic products like bottles and fuel tanks.
- Extrusion: Ideal for creating plastic sheets, tubes, and pipes.
- Thermoforming: Used to mold heated plastic sheets into specific shapes, such as disposable trays.
- Rotational Molding: Suitable for large, hollow objects like tanks and playground equipment.
Material Selection
Different types of plastics are used in manufacturing, depending on the product’s requirements:
- Polyethylene (PE): Found in bags, containers, and household items.
- Polypropylene (PP): Used in automotive parts and medical devices.
- Polyvinyl Chloride (PVC): Common in pipes and construction materials.
- Polystyrene (PS): Used in food packaging and disposable utensils.
- Acrylonitrile Butadiene Styrene (ABS): Popular in electronic casings and toys.
Quality Control
Manufacturers ensure product quality through stringent testing, including:
- Durability and strength tests
- Chemical resistance analysis
- Environmental impact assessments
- Safety and compliance checks with regulatory standards
Importance of Plastic Product Manufacturing
Plastic products play an integral role in modern life by providing durability, flexibility, and cost-efficiency. The industry contributes to various aspects of society and the economy.
Key Benefits:
- Versatility: Plastics are used in diverse applications, from consumer goods to industrial components.
- Cost-Effectiveness: Compared to alternative materials, plastics are often cheaper to produce.
- Lightweight Nature: Reduces transportation costs and energy consumption.
- Recyclability: Advances in recycling help reduce environmental impact.
- Innovation and Customization: Plastics allow for innovative product designs and modifications.
Key Features of a Well-Functioning Plastic Manufacturing Facility
A well-optimized plastic manufacturing plant ensures efficiency, sustainability, and high product quality.
Characteristics of an Effective Facility:
- Advanced Machinery: Utilization of state-of-the-art production equipment.
- Skilled Workforce: Trained personnel to oversee operations and quality control.
- Sustainable Practices: Implementation of eco-friendly production methods.
- Safety Standards Compliance: Adherence to industry regulations and workplace safety protocols.
- Supply Chain Efficiency: Robust logistics for material sourcing and product distribution.
Why Plastic Manufacturing Is Essential for Sustainable Development
Despite concerns over plastic waste, the industry continues to evolve with sustainable solutions that contribute to economic and environmental well-being.
Factors Driving the Importance of Plastic Manufacturing:
- Economic Growth: Creates jobs and supports various industries.
- Technological Advancements: Innovations in biodegradable plastics and recycling processes.
- Energy Efficiency: Modern plastics reduce energy consumption in various applications.
- Healthcare and Safety: Plastic materials are vital for medical devices and protective equipment.
- Infrastructure Development: Used in construction materials, plumbing, and insulation.
Challenges Facing Plastic Product Manufacturing
The plastic manufacturing industry faces several challenges that affect production, sustainability, and consumer perception.
Common Challenges:
- Environmental Concerns: Plastic pollution and waste management issues.
- Regulatory Compliance: Adhering to stringent environmental and safety regulations.
- Raw Material Costs: Fluctuating prices of petroleum-based resins.
- Recycling Limitations: Difficulty in processing certain types of plastics.
- Public Perception: Increasing consumer demand for eco-friendly alternatives.
How to Improve Plastic Manufacturing Efficiency
Enhancing plastic production efficiency requires adopting new technologies, sustainable practices, and industry collaboration.
Strategies for Better Manufacturing:
- Investment in Recycling: Developing effective plastic recycling programs.
- Use of Biodegradable Plastics: Shifting towards eco-friendly material options.
- Energy-Efficient Production: Implementing energy-saving manufacturing techniques.
- Automation and AI: Utilizing smart manufacturing for precision and waste reduction.
- Research and Development: Innovating new plastic composites with better environmental performance.
Investment Opportunities in Plastic Manufacturing
The plastic industry presents numerous investment prospects, from raw material production to finished goods and recycling services.
Business Models:
- Eco-Friendly Plastic Production: Manufacturing biodegradable and recycled plastics.
- Specialty Plastic Products: Developing niche products for medical, aerospace, or automotive industries.
- Plastic Waste Management: Establishing advanced plastic recycling plants.
- Injection Molding Services: Providing contract manufacturing for customized plastic parts.
- Smart Packaging Solutions: Integrating technology into packaging for enhanced functionality.
Future Trends in Plastic Product Manufacturing
The future of plastic manufacturing is driven by sustainability, technological advancements, and changing consumer preferences.
Emerging Trends:
- Bioplastics: Increasing use of plant-based plastic alternatives.
- 3D Printing: Custom plastic production with minimal waste.
- Smart Plastics: Integration of sensors and self-healing materials.
- Circular Economy: Focus on plastic reuse and recycling.
- Global Regulations: Stricter policies to reduce plastic waste and encourage sustainable practices.
Plastic Product Manufacturing: A Comprehensive Guide to Understanding, Processes, and Industry Trends
Plastic product manufacturing is a cornerstone of modern industry, providing essential materials for various applications, from packaging to automotive parts and medical devices. This sector plays a critical role in global supply chains, offering durable, lightweight, and cost-effective solutions across multiple industries. Whether you are a business owner, entrepreneur, or consumer, understanding plastic manufacturing processes, industry trends, and sustainability concerns is crucial.
This guide explores the definition and types of plastic products, manufacturing processes, industry applications, governance, challenges, and emerging trends.
Understanding Plastic Product Manufacturing
Plastic product manufacturing involves converting raw plastic materials into finished goods using different processing techniques. These products vary in complexity, functionality, and durability, catering to industries such as packaging, construction, automotive, healthcare, and consumer goods.
Key Aspects of Plastic Manufacturing:
- Types of Plastics: Thermoplastics (e.g., polyethylene, polypropylene) and thermosetting plastics (e.g., epoxy, phenolic) serve different industrial needs.
- Production Techniques: Manufacturing methods such as injection molding, extrusion, and blow molding determine the product's properties and application.
- Material Sourcing: Raw plastics are derived from petroleum-based sources or bio-based alternatives.
- Quality Control: Industry standards and testing ensure the safety, durability, and compliance of plastic products.
- Sustainability Measures: Recycling, biodegradable plastics, and energy-efficient production are growing trends in plastic manufacturing.
Importance of Plastic Products in Society
Plastic products are indispensable in modern life, contributing to economic growth, technological advancements, and enhanced living standards. Their lightweight and versatile nature makes them ideal for countless applications.
Key Benefits of Plastic Products:
- Durability and Flexibility: Plastics offer resistance to corrosion, moisture, and wear, extending product lifespan.
- Cost-Effectiveness: Compared to alternative materials, plastics provide affordable solutions for mass production.
- Lightweight Nature: Reduced weight lowers transportation costs and improves energy efficiency.
- Innovation and Design: Plastic molding technologies enable complex, customizable designs for various industries.
- Sustainability Potential: Advances in biodegradable plastics and recycling enhance eco-friendliness.
Types of Plastic Products
Plastics are classified based on their composition, properties, and applications. The selection of plastic materials depends on factors such as durability, temperature resistance, and environmental impact.
1. Consumer Plastic Products
Used in everyday items, including packaging, household goods, and personal care products.
- Bottles and containers
- Bags and wraps
- Toys and electronics casings
2. Industrial and Automotive Plastics
Designed for high-performance applications in manufacturing and transportation.
- Car dashboards, bumpers, and fuel tanks
- Industrial machine components
- Aerospace parts
3. Medical and Healthcare Plastics
Essential for ensuring hygiene, safety, and reliability in healthcare settings.
- Surgical instruments and implants
- IV bags and tubing
- Pharmaceutical packaging
4. Construction and Infrastructure Plastics
Used for durability and insulation in building projects.
- PVC pipes and fittings
- Roofing sheets and insulation materials
- Flooring and wall panels
Plastic Manufacturing Processes
Different manufacturing techniques determine the physical and chemical properties of plastic products. Each method is tailored to specific applications, ensuring efficiency and quality.
1. Injection Molding
A widely used process where melted plastic is injected into molds to create solid shapes.
- Commonly used for packaging, medical devices, and automotive parts.
- High production speed and precision.
2. Extrusion
A continuous process where melted plastic is forced through a die to create long, uniform shapes.
- Used for pipes, tubes, and films.
- Suitable for high-volume production.
3. Blow Molding
A process for making hollow plastic objects by inflating melted plastic inside a mold.
- Used for bottles, containers, and tanks.
- Cost-effective for large production runs.
4. Rotational Molding
A technique where plastic is heated and rotated inside a mold to form large, hollow objects.
- Used for water tanks, playground equipment, and large containers.
- Produces durable and seamless products.
5. 3D Printing
An emerging technology where plastic is layered to create custom objects.
- Used for prototyping, medical implants, and small-scale production.
- Allows for design flexibility and minimal waste.
Industry Governance and Regulations
Governments and international bodies regulate plastic manufacturing to ensure safety, quality, and environmental responsibility.
Governance Structures in Plastic Manufacturing:
- Environmental Protection Agencies: Regulate emissions, waste management, and recycling initiatives.
- Health and Safety Standards: Organizations such as FDA and ISO ensure product safety and compliance.
- Trade and Industry Associations: Groups like the Plastics Industry Association advocate for industry best practices and policies.
- Recycling and Waste Management Laws: Governments implement bans on single-use plastics and promote circular economy practices.
Challenges in Plastic Manufacturing
Despite its benefits, plastic manufacturing faces several challenges related to sustainability, resource management, and innovation.
Common Challenges:
- Environmental Concerns: Plastic waste pollution and non-biodegradable materials raise ecological issues.
- Supply Chain Disruptions: Dependency on petrochemical industries and raw material shortages affect production.
- Recycling Limitations: Inconsistent recycling policies and lack of infrastructure hinder effective waste management.
- Consumer Perception: Growing demand for eco-friendly alternatives shifts industry trends toward biodegradable plastics.
- Technological Adaptation: Implementing energy-efficient and innovative manufacturing techniques requires investment.
Investment Opportunities in Plastic Manufacturing
The plastic industry offers diverse investment prospects, from raw material production to recycling solutions and biodegradable alternatives.
Key Investment Areas:
- Biodegradable and Bio-Based Plastics: Developing sustainable materials for packaging and consumer goods.
- Advanced Recycling Technologies: Enhancing plastic waste management through chemical and mechanical recycling.
- Automation and Smart Manufacturing: Implementing AI-driven production for cost efficiency and quality control.
- Medical Plastics: Investing in healthcare-related plastic products for growing global demand.
- 3D Printing Innovation: Supporting additive manufacturing for customizable and specialized applications.
Future Trends in Plastic Manufacturing
The plastic industry is evolving with technological advancements, sustainability initiatives, and regulatory changes.
Emerging Trends:
- Circular Economy Practices: Recycling and reusing plastics to minimize environmental impact.
- Nanotechnology in Plastics: Enhancing strength, flexibility, and heat resistance of plastic materials.
- AI and Automation: Improving precision, efficiency, and waste reduction in manufacturing processes.
- Eco-Friendly Packaging: Rising demand for compostable and biodegradable packaging solutions.
- Global Regulations and Compliance: Stricter policies driving innovations in sustainable plastic production.
Plastic Product Manufacturing: A Comprehensive Guide to Understanding Its Role and Function
Plastic product manufacturing is a crucial industry that influences multiple sectors, from packaging and construction to healthcare and consumer goods. Whether you are interested in understanding its processes, significance, or the technological advancements shaping its future, this guide provides an in-depth insight into the plastic manufacturing industry.
What Is Plastic Product Manufacturing?
Plastic product manufacturing refers to the production of plastic materials and items using various processes such as injection molding, extrusion, blow molding, and thermoforming. These methods transform raw plastic materials into finished products used in everyday life, including packaging, automotive components, medical devices, and household goods.
Why Plastic Product Manufacturing Is Essential
The plastic manufacturing industry is vital for modern society. It offers solutions for lightweight, durable, and cost-effective products across diverse industries. The significance of plastic manufacturing is highlighted through several key aspects:
Material Versatility
- Plastics can be molded into a wide variety of shapes and sizes.
- They offer flexibility, durability, and lightweight properties that make them superior to traditional materials like metal and glass.
Economic Contribution
- The plastic industry generates millions of jobs worldwide, from production to research and development.
- It drives innovation, supporting industries such as automotive, healthcare, and electronics.
Sustainability and Recycling Efforts
- Advancements in biodegradable plastics and recycling technologies are reducing environmental impact.
- Circular economy initiatives are promoting plastic waste management and reusability.
Key Components of a Successful Plastic Manufacturing Process
Strategic Planning
A plastic manufacturing company must have a well-defined strategy, including:
- Material Selection: Choosing the right type of plastic based on application needs (e.g., polyethylene, polypropylene, polystyrene).
- Process Optimization: Enhancing efficiency and reducing production costs through automation and lean manufacturing techniques.
- Sustainability Measures: Implementing eco-friendly practices such as using recycled materials and energy-efficient machinery.
Advanced Manufacturing Techniques
The industry utilizes various production methods, including:
- Injection Molding: Used for high-volume production of plastic parts with precision.
- Extrusion: Produces continuous shapes such as pipes and sheets.
- Blow Molding: Commonly used for making plastic bottles and containers.
- 3D Printing: A growing technology for custom and complex plastic components.
Strong Governance Structure
A successful plastic manufacturing company requires effective leadership and transparency, including:
- Regulatory Compliance: Adhering to environmental and safety regulations such as FDA, EPA, and ISO standards.
- Quality Control Measures: Ensuring product consistency through rigorous testing and inspection protocols.
- Workforce Training: Investing in skilled labor and continuous education to keep up with industry advancements.
Challenges Faced by the Plastic Manufacturing Industry
Environmental Concerns
- Plastic waste and pollution remain significant challenges.
- Regulatory pressures to reduce single-use plastics and promote sustainable alternatives.
Raw Material Price Fluctuations
- Dependency on petroleum-based raw materials makes the industry vulnerable to price changes.
- Efforts to develop bio-based plastics to mitigate reliance on fossil fuels.
Technological Gaps and Automation
- Many manufacturers struggle with adopting new technologies due to high implementation costs.
- The transition to Industry 4.0, including IoT and AI-driven manufacturing, is crucial for competitiveness.
The Role of Private Entities in Plastic Manufacturing Development
Public-Private Partnerships (PPPs)
- Collaborations between governments and private firms to develop sustainable plastic solutions.
- Investment in waste management and recycling infrastructure to tackle plastic pollution.
Corporate Social Responsibility (CSR)
- Companies investing in eco-friendly initiatives, such as biodegradable plastics and reusable packaging solutions.
- Sponsoring research and development in sustainable polymer alternatives.
Technological Innovation
- Adoption of smart manufacturing techniques to enhance efficiency and reduce waste.
- Use of blockchain for transparent supply chain management in the plastic industry.
Benefits of a Well-Managed Plastic Manufacturing Industry
Product Innovation and Customization
- Advanced molding techniques allow for the production of complex and customized plastic parts.
- Industries like healthcare benefit from medical-grade plastics used in implants, prosthetics, and surgical instruments.
Economic Growth and Employment
- The plastic sector supports various industries, indirectly creating job opportunities worldwide.
- Local and global markets thrive due to the affordability and accessibility of plastic products.
Environmental and Sustainability Efforts
- Circular economy models focus on recycling and reusing plastic waste efficiently.
- Innovations in biodegradable plastics are reducing the ecological footprint of plastic manufacturing.
Future Trends in Plastic Product Manufacturing
Smart Factories and Digital Transformation
- Integration of AI and machine learning for quality control and predictive maintenance.
- IoT-enabled machinery to optimize production processes and reduce downtime.
Sustainable Material Development
- Growth in bio-based and biodegradable plastics to replace conventional petroleum-based materials.
- Research into nanotechnology to enhance plastic properties and recyclability.
Increased Collaboration and Policy Support
- Stronger alliances between manufacturers, policymakers, and environmental groups to drive sustainable innovation.
- Government incentives for companies that adopt eco-friendly manufacturing practices.
How does product liability insurance benefit plastic manufacturers?
Product liability insurance protects your business from financial loss if a product you manufacture causes harm or damage. This coverage helps pay for legal defense costs, settlements, or judgments if your product is found to be defective and causes injury or property damage.
Are there specialized insurance programs for plastic manufacturers in California?
Yes, there are insurance programs specifically designed for plastic manufacturers that address unique industry risks, such as equipment breakdowns, defective parts, and fire hazards. These specialized programs offer coverage tailored to the specific needs of plastic manufacturing operations.
What types of insurance are essential for plastic product manufacturers in California?
- General Liability Insurance: Protects against third-party claims of bodily injury or property damage occurring on your premises or due to your products.
- Product Liability Insurance: Covers legal fees, settlements, or judgments arising from injuries or damages caused by defective products.
- Workers' Compensation Insurance: Mandatory in California, this covers medical expenses and lost wages for employees injured on the job.
- Commercial Property Insurance: Safeguards your facility, equipment, and inventory against risks like fire, theft, or natural disasters.
- Equipment Breakdown Coverage: Covers repair or replacement costs for machinery and equipment that break down due to mechanical issues.
- Business Interruption Insurance: Provides financial support if your operations are temporarily halted due to a covered event, helping to cover lost income and ongoing expenses.
REQUEST A QUOTE
Speak with a CA Workers Compensation Insurance specialist today!
Learn More About Workers Comp. Insurance
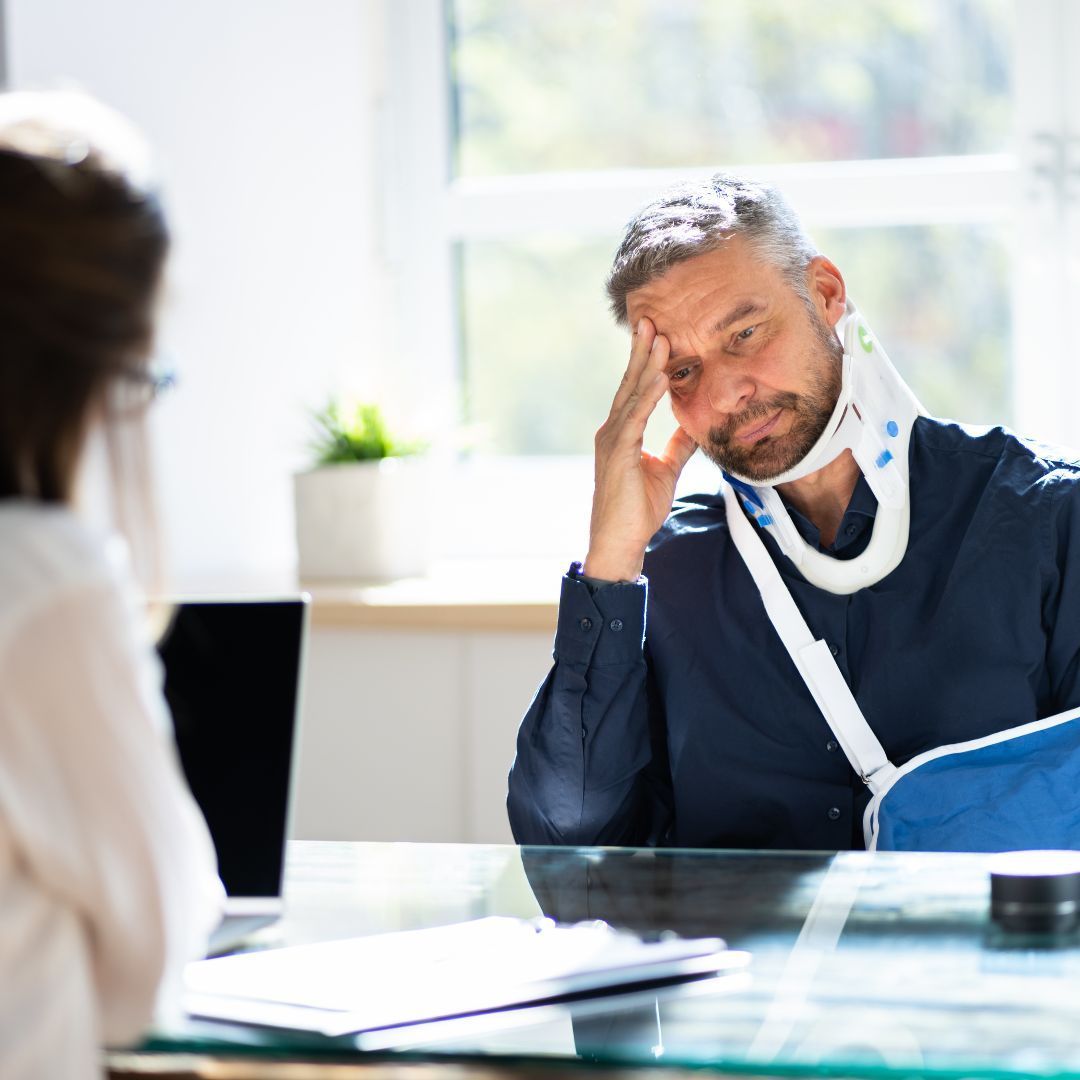
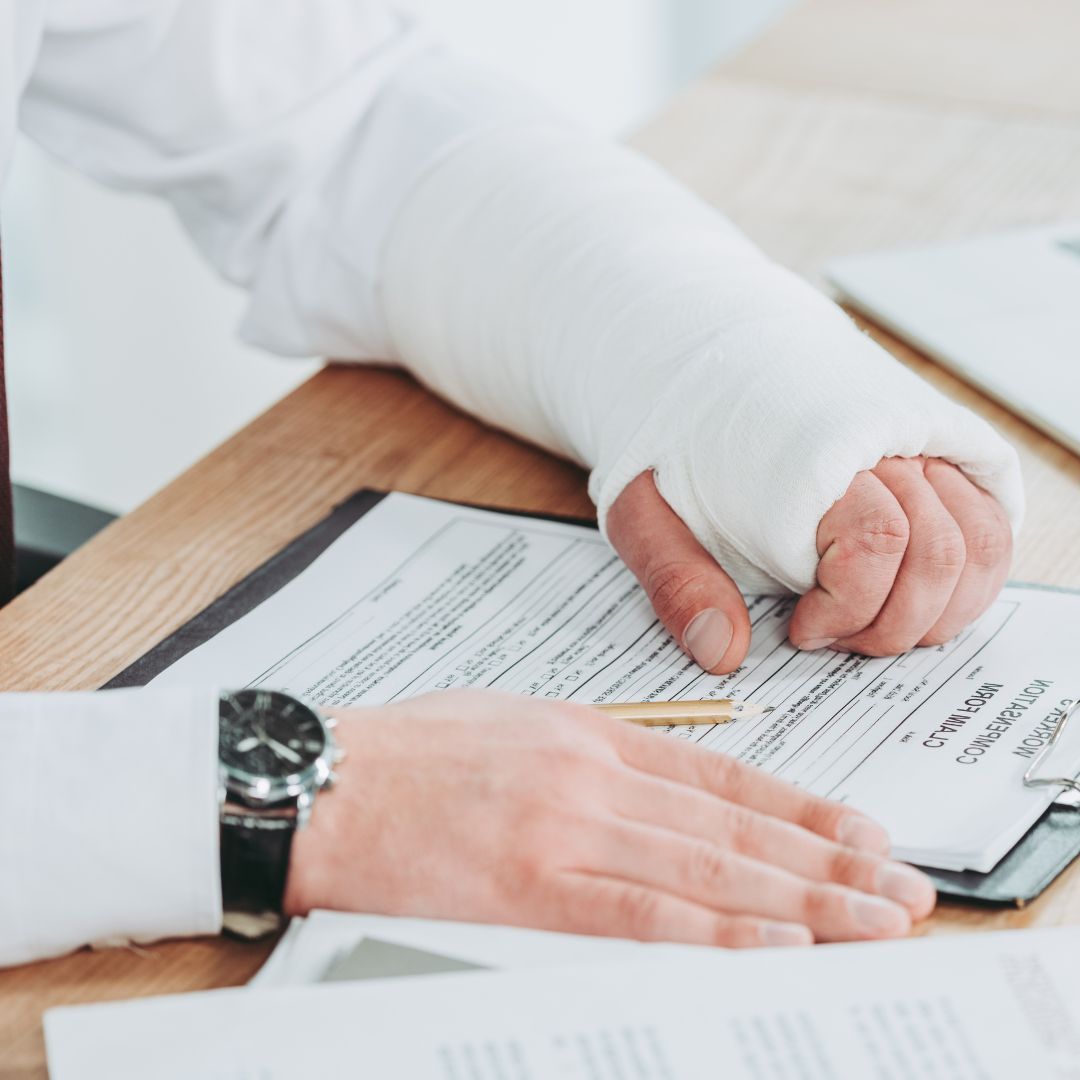